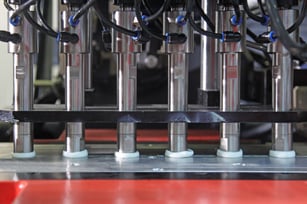
Carbon buildup and contamination require screw pulls. Although screw pulls may be necessary on a periodic basis, manufacturers that fail to take preventive measures will suffer from unplanned downtime. Being forced to clean your screws more frequently than needed is a costly impact your facility can’t afford.
Here are two methods to effectively purge your extrusion blow molding machine:
Method #1: Use A High-Quality Purging Compound
One of the most effective ways to purge your extrusion blow molding machine is to use a purging compound. In many cases, transitions are dramatically shortened with the use of a purging compound because they eliminate residue and contamination.Extrusion blow molding heads and accumulators are, by design, low-pressure areas. The low-flow or low-pressure environment of extrusion blow molding leads to difficulty cleaning certain areas. Since mechanical purging compounds require maximum pressure, they’re not always the best choice for this application. Instead, try using a chemical purging compound.
When cleaning screws for extrusion, it’s important that you use the right product and purging process. Using the wrong chemicals or tools may ruin screws or die heads and lead to serious production problems.
The product grade you’ll need depends largely on the thermoplastic resin being purged and its processing temperature. If contamination is an issue for your facility, your supplier may recommend a different grade.
Purging procedures for the extrusion blow molding process vary depending on the purging product you’re using. If you’re unsure on how to most efficiently clean your extrusion blow molding machine, it’s best to reach out to your purging compound supplier.
Method #2: Practice Preventive Purging Procedures
Many plastic processing companies only using purging compounds when it’s absolutely necessary. But engaging in this type of purging “process” leads to reduced profitability and efficiency.
Adopting preventive purging practices not only saves your facility from machine downtime, it also reduces your scrap rates, customer rejects and line shutdowns. You can’t afford to wait to run purging compounds until the last minute because, by that time, you’re already suffering from contamination issues or color streaks.
Using a purging compound at regular intervals prevents contamination from the beginning. Typically, it only takes one to two system capacities of purging compound to prevent contamination. Most operators would rather have planned purging-related downtime than an unplanned screw or head pull.
There are three main benefits to implementing a preventive maintenance program and purging process at your facility, including:
1. Preventing the buildup of color and carbon contamination
2. Reducing excessive purging time and material waste at the end of production runs
3. Limiting the frequency of screw pulls and minimizing the time and effort required to pull and manually clean your screw
Excessive downtime negatively impacts your ability to meet or exceed business projections. By using a purging compound and taking preventive measures, you will maximize efficiency and productivity at your facility.
Learn more about increasing profitability with proven and effective purging procedures
Comments