In injection molding, warpage is a common defect a processor could deal with. Warpage is an issue especially before the process is fine tuned to the product. Warpage occurs for a variety of different reasons but can be identified when a part has the shape of the cavity but some or all of it exhibits distortion from the parameters of a quality part. This distortion can range from barely visible defects to a part appearing noticeably distorted.
There are 3 typical causes of warpage. Knowing the cause will help you address and stop the defects.
Machine – Warpage could be due to excessive internal strain on the molded part. In this case, you could try and reduce the injection pressure, reduce the screw forward time, increase the cooling time. It’s likely that the process could be the main issue causing warpage. There are several factors to consider but the process is a likely place to start diagnosing this issue.
Mold – There are also several causes of warpage that could be linked to your mold or mold design. The flow rate of the water channels running through the mold could be too low causing too much heat on the part and not allowing the part to fully cool during the cooling time process. The cooling circuits in the mold could also be unbalanced which could cause certain cavities to demonstrate warpage while other are up to quality standards. The gates on the mold could also be improperly located or designed.
Material – In some cases the material could be the cause of warpage. If the part is not designed with that particular material in mind to mold with it could cause issues. Also, if the material is filled with anything the % of filler and the type of filler can play a role into warpage of the finished part.
It is important to understand and address the cause of the problem instead of treating the symptoms. If you review your process with these three possible causes in mind, you will be in a better position to lower your scrap and reduce warpage.
Learn more about how to reduce production downtime and protect your profits with a purging compound.
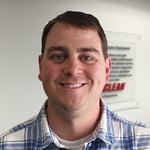
Jeremy Cooley is an Asaclean Technical Service Representative & Purging Expert living in South Carolina. He's worked in injection molding & purging for over 15 years, and frequently presents at national plastics trade shows and conferences.
Comments