For shot-to-shot repeatability there are many factors that play an important role and many test and studies that can be performed to reveal problematic contributions to inconsistent part-weights. We are going to talk about one of these important factors in this segment which is the cushion.
We are all very familiar with this word and what it defines in our process but furthermore this “Actual” needs to be tracked and monitored by setting up tolerances to signal you or alarm the machine when if it deviates too far which will affect your shot weight.
The cushion is the plastic that is left in front of the screw at the end of your pack/hold. It is very important to have this remaining plastic for the screw to transfer the plastic pressure into your cavity and pack out the part. Without this remaining plastic the screw would bottom out on the barrel and you would lose control over the packing pressure and your shot-to-shot dimensional qualities.
1.) Evaluate the Condition of Your Check Ring SealThis will let us know the current condition of your check-ring and how much plastic is getting by each time you inject forward. We start here first because we want to confirm that your check ring can provide a consistent seal and cushion.
2.) Perform a Check Ring StudyThis is a quick and easy study to determine the current state of your check-ring seal. For this study you will need to turn pack/hold off and make 10 first- stage only injection parts that are short. Make 10 fill only parts (short shots). Weigh each shot (including parts and runner). Add all the weights up and divide by 10 to get an avg. weight. Then take your heaviest part and subtract by the lightest part to get a difference.
Take that difference divide by the Average from before and then x 100 to get the percent of variation from the avg. weight. This variation % is what is important. Typically, an acceptable range should be below 2%. When the screw moves forward during injection and the check-ring seats it forms a tight seal only allowing very minimal or no plastic to squeeze by.
If you find that you are below this range than you can deduce that your check ring has a proper seal when injecting forward and are good to move forward to production or further diagnosis.
3.) Use a Powerful Commercial Purge Compound
If you find that you are above this mark, you should stop and purge immediately to clean the check ring area there may be degraded material or carbon build up in this area causing the check-ring to not seat properly.
ASACLEAN makes a fantastic purging compound called EX Grade which is our maximum scrubbing product designed to specifically remove any build up on the screw and barrel. Using this product and our purging procedures (along with speaking with one of our technical advisors), we can target this specific area to get an effective and thorough cleaning for a better check-ring seal and shot-to-shot repeatability.
Ready to reduce your production downtime to protect your profits? Learn more about how purging compounds and process efficiency work in tandem.
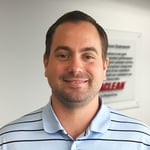
Hank Moeller is an Injection Molding and Purging Expert with over 20 years of experience in a processing environment.
Comments