The sheet extrusion process is fraught with challenges that can escalate costs and reduce efficiency at a moment's notice. One such challenge is contamination issues, like black specks and color streaks, which can be time-consuming to clean. This often leads to significant material waste and affects overall facility operations. But what if these problems could be mitigated more effectively? Implementing a purge program can be a game-changer in this regard. Let's explore how a purge program can positively impact customer satisfaction, materials management, and conversion costs.
1. Boosting Customer Satisfaction with Fewer DefectsIn the intricate sheet extrusion process, any defect can inadvertently increase the risk of these flaws reaching the customer. To mitigate this, extensive space is often dedicated to scrutinizing sheet pallets to identify the onset of these defects. To err on the side of caution, additional materials are frequently scrapped. However, should these precautionary measures prove insufficient, they lead to customer grievances and other expenditures for the quality department to address these issues at the customer's location. This disruption also adversely impacts the production schedule, resulting in a detrimental cycle of shortened production runs and more frequent changeovers, which are ripe opportunities for further contamination. This cycle of inefficiencies often culminates in delayed and incomplete deliveries, escalating outbound freight costs and affecting overall customer satisfaction. A purge program helps significantly reduce these risks, ensuring higher quality control and consistent delivery schedules.
2. Optimizing Material ManagementA purge program doesn't just address production inefficiencies; it also plays a crucial role in inventory management. By reducing the amount of scrap generated, you can avoid the need for excessive storage space and manage your warehouse more effectively. This approach is especially beneficial for dealing with low-volume lots or specific customer specifications that limit recycling options. Consequently, this leads to fewer purchases of raw materials and reduced inbound freight costs, making your materials department more efficient and cost-effective.
3. Cutting Down Conversion CostsBeyond the visible waste, there are hidden costs in sheet extrusion, notably in electricity consumption and overtime. Each pound of material that fails to convert into a sellable product on the first attempt is a drain on resources. Purge programs help minimize heavy electricity-consuming equipment running time like motor grinders and extruders. Additionally, it reduces the likelihood of overtime caused by extended production hours or extensive maintenance shutdowns for cleaning, thus enhancing overall production efficiency.
A Collaborative Approach to Improvement
Implementing a purge program isn't just a task for the production team; it requires a concerted effort across various departments – purchasing, quality, materials, finance, and maintenance. Understanding the root causes of production inefficiencies and addressing them through a comprehensive purge program can lead to substantial savings and operational improvements.
Conclusion
By setting up a purge program, with the guidance of our purging expert, and garnering support from all departments, companies in the plastic processing industry can preempt many common challenges. This ensures a more efficient production process and leads to significant cost savings and improved customer satisfaction.
Looking to implement a purge program in your plastic sheet extrusion process? Contact our team of experts for tailored solutions that can transform your production efficiency.
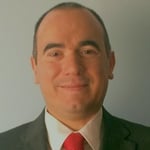
Hector Sanchez, the National Sales Manager at Asaclean - Asahi Kasei Plastics North America, leverages his extensive processing expertise to assist extruders and molders in achieving their operational goals. With a focus on reducing scrap and increasing profits, Hector's in-depth knowledge of Asaclean's Purging Compounds has made him a pivotal figure in the industry. Beyond his primary role, Hector is a dynamic speaker, regularly sharing his insights and strategies at webinars and tradeshows nationwide. His innovative approaches and dedication to customer success have established him as a valued leader and mentor in the plastic industry.
Comments