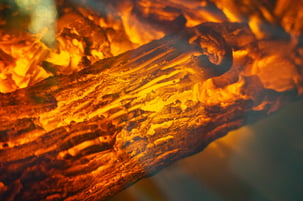
Shear heat can be a hidden culprit behind inefficiencies in your injection molding process, causing costly downtime and defects in molded parts. Addressing this issue is key to boosting productivity and improving overall part quality. Here are three quick tips to help you troubleshoot and resolve shear heat issues during injection molding.
1. Start With the Nozzle Tip
If you're facing shear heat problems such as uneven melt flow, excessive part warpage, or inconsistent part quality, the nozzle tip on your injection molding machine should be your first area of focus. Ensure the nozzle tip orifice is about 75-85% the size of the sprue bushing orifice. This simple adjustment can significantly reduce shear heat and improve melt flow.
2. Inspect the Hot Runner System
Another key area to examine is the hot runner system. Check for any blockages that might disrupt plastic flow. Adding an overflow tab can help reduce the likelihood of cold slugs entering the gate, which can exacerbate shear heat issues. Proper purging of your hot runner system is essential, not only to prevent future problems but also to ensure smooth, reliable operation of your process.
3. Optimize Gate Dimensions
Ensure your gate dimensions are about 75-85% of the nominal wall thickness to promote even flow into the part. If you're working with a resin prone to jetting, deflecting the material by bouncing it off a wall or sturdy boss can minimize shear heat and improve part quality.
Bonus Tip: Check Mold Cooling
If adjusting the nozzle tip, hot runner, and gate dimensions doesn't resolve the issue, review your cooling system. Proper water flow through the mold is crucial for maintaining an even temperature, which helps regulate shear heat and keeps your process stable.
Need More Help?
If you're still experiencing shear heat issues, contact us for expert guidance. We’ll help you identify the problem and optimize your injection molding process for maximum efficiency.
Learn how to reduce machine downtime with five quick purging compound tips for your injection molding application.
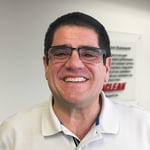
Eric Despotovich, an esteemed Asaclean Purging Expert and Technical Sales Representative, brings over 40 years of processing experience to his role. With over 18 years of dedication to our company, Eric has become a cornerstone of our sales team, renowned for his commitment to client success. His extensive industry knowledge and genuine passion for helping clients make him a trusted advisor in optimizing their operations. Eric's approach is characterized by deeply understanding each client's unique challenges, ensuring tailored solutions that drive efficiency and profitability.
Comments