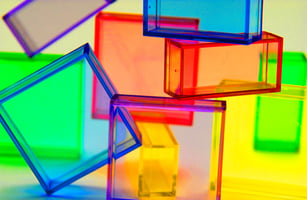
Production downtime and materials degradation negatively impact your bottom line. Plus, machine failures result in missed deadlines, unhappy customers and lost profit.
Your profits are particularly at risk when you’re working with expensive, high-temperature resins. To protect your bottom line, you need to reduce the risk associated with contaminated processing machines and material scrap. This means you should properly purge these resins from your machines with high-quality purging compounds.
Here are three tips for effectively purging high-temperature resins from your molding machines to avoid wasting materials and money.
1. Use A High-Temperature-Grade Purging Compound
Super engineering resins run at high operating temperatures may require different grades of purging compounds. High-temperature-grade purging compounds are designed to maintain thermal stability at very high processing temperatures and more effectively facilitate material and color changeovers.
Using the wrong grade of purging compound results in sub-optimal purging. This puts your machines at risk for resin buildup, which can cause encapsulated materials to degrade. Even worse, carbon buildup may cause your machine to fail, which can lead to hours of downtime. Additionally, purging compounds designed for the wrong temperature may leave behind residue, or may themselves degrade at very high temperatures.
For these reasons, make sure your operators use purging compounds developed for use with the materials and temperatures you’re working with.
2. Purge Machines Before Carbon Appears
When you’re processing at very high temperatures, resins degrade more quickly. If your resins degrade in the barrel, your scrap rates are going to rise. Having to scrap components molded with high-temperature resins, which can cost more than $30 per pound, is detrimental to your profitability.
Resin degradation happens before you can see the carbon buildup in your machines. If you wait for visual evidence of carbon buildup, it may be too late for purging compounds to remove the contamination. You will need a screw pull and manual cleaning.
Avoid having to scrap costly materials by implementing preventative purging. This helps you limit the buildup of carbon and protect your bottom line.
3. Clean Your Machines With High-Temperature Purging Compounds Before Reducing Heat
When transitioning from high-heat resins to lower-heat resins, it’s helpful to bridge the temperature range by starting with purging compounds developed for high temperatures. While the machine components are cooling, you may also need to flush and add a new barrel capacity depending on the temperature and the time it takes to reduce heat for the next resin.
Going through proper temperature-transitioning purging procedures helps you save money by limiting your usage of the more expensive resin.
Work Faster And More Effectively With Proper Purging
Using the right purging compounds and executing the proper purging processes helps to avoid machine downtime and wasted materials. Taking a preventative approach to your machine cleaning means you can more effectively transition between the different resins and colors your customers require.
By flexibly accommodating your customers’ needs in a cost-effective way, you gain a competitive edge and protect your bottom line.
Discover more ways to reduce thermoplastic molding scrap.
Comments