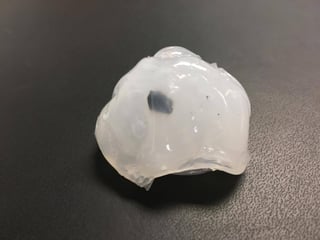
The creation of black / brown specks is one of the most common defects you’ll find in injection molding. This defect can often be a nightmare for processors as they can appear and quickly disappear at irregular intervals during the molding process. Black specks tell the processor that there is certainly some level of contamination present within the system.
Black / brown specks can almost always be attributed to a heat or residence time causation. There are times when a post-molded part can come in contact with grease or dirt on the molding surface. But if the defect is within the molded part then a processor can be sure that there is contaminated material present in the system.
Specks can be caused by a few different factors including the following:
- Overheating of the processing resin causing degradation
- Excessive shearing of the resin caused by back pressure and incorrect screw surface speeds
- Too much residence time in the barrel resulting in degradation
- Or the presence of a former resin that is heat sensitive degrading within the processing resin
It can be tough to get control of degraded material with processing adjustments alone. A good commercial grade purging compound like Asaclean is the best solution for purging the system of degraded material so the processor can reestablish the process with a clean screw and barrel. It is always a good idea to use a purging compound when changing over resins that will run on the same press. This will ensure that the previous resin that could be more heat sensitive is not lingering in the system to possibly cause problems with the next run.
Learn about the importance of implementing proper purging procedures by downloading this free industry guide.
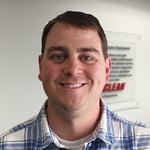
Jeremy Cooley is an Asaclean Technical Service Representative & Purging Expert living in South Carolina. He's worked in injection molding & purging for over 15 years, and frequently presents at national plastics trade shows and conferences.
Comments