Automotive lightweighting has become a significant focus for manufacturers seeking to improve fuel efficiency and reduce emissions. As the industry shifts toward lightweight materials like Asahi Kasei Plastics' Leona SG, purging compounds like Asaclean® provide an essential solution to overcoming common processing challenges. In this blog, we'll explore how purging compounds can support the production of lightweight automotive components while maintaining efficiency and quality.
- Material Compatibility for Multi-Material Components: Lightweight automotive components often involve using multiple materials, such as combinations of polypropylene, nylon, and other advanced resins. Purging compounds like Asaclean® are compatible with various materials, including SG, making them ideal for multi-material components. This versatility ensures that purging compounds can be seamlessly integrated into your production process, helping to reduce material waste and contamination.
- Minimizing Color Contamination: Reducing color contamination is critical because automotive components require precise color matching and consistency. Purging compounds like Asaclean® can help minimize color contamination during material and color changeovers, ensuring that your lightweight components meet the highest quality standards. Incorporating purging compounds into your changeover process can significantly reduce scrap rates and improve overall efficiency.
- Optimizing Injection Molding for Lightweight Components: Injection molding is a common method for producing lightweight automotive components. Purging compounds can be crucial in optimizing the injection molding process by ensuring your machines are clean and residue-free. Incorporating purging compounds into your maintenance routine can prevent issues like carbon buildup and material degradation, ultimately improving cycle times and part quality.
- Enhancing Material Flow and Consistency: Lightweight materials often require specific processing parameters to ensure optimal material flow and consistency. Purging compounds like Asaclean® can help maintain the ideal processing conditions by removing contaminants and residual materials from your machines. This results in a more consistent material flow, crucial for producing high-quality, lightweight automotive components.
- Supporting Sustainability Initiatives: The automotive industry emphasizes lightweighting to improve fuel efficiency and reduce emissions, aligning with broader sustainability goals. Purging compounds can support these objectives by reducing material waste, minimizing energy consumption during changeovers, and extending the lifespan of your machinery. By adopting purging compounds like Asaclean®, you can enhance your lightweight component production and contribute to a more sustainable future for the automotive industry.
- Maintaining Optimal Processing Temperatures: Lightweight materials often require precise processing temperatures to achieve the desired properties and performance. Purging compounds like Asaclean® can help you retain these optimal temperatures by ensuring your machines are free from contaminants and material residue. This results in more consistent processing conditions, essential for producing high-quality, lightweight automotive components.
Conclusion: As the automotive industry prioritizes lightweighting, purging compounds like Asaclean® offers an essential solution for overcoming common processing challenges. By incorporating purging compounds into your production process, you can support the creation of lightweight components while maintaining efficiency and quality. From material compatibility to sustainability initiatives, purging compounds provide numerous benefits that can help you succeed in the competitive automotive market.
Interested in solving your molding issues with Asaclean? Request a Free Sample of Asaclean Today.
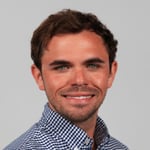
Tom Hanvey is the Product Manager for Sustainability for Asahi Kasei Plastics North America. Before joining APNA, he worked as the Senior Marketing Manager for Asaclean Purging Compounds. He's worked in the plastics industry for over 8 years and focuses on recyclable resins and on the inbound marketing side, providing easy-to-digest content to processors looking for an edge on their competition.
Comments