If you are a blown film manufacturer, then you know how hard it is to complete a color change through a spiral die going from dark to light. Most blown film manufacturers hate to purge their machine when changing colors, because they inevitably lose the bubble and would have to go through the effort of restringing it. They would prefer to “just run resin through” to “clean” the machine. This is not the most efficient or economical way to purge these machines.
Here are 5 tips on how to maintain a bubble during a color change on the fly:
- Choose the right grade of purge for the right resin. Such as our Asaclean NL for LLDPE or LDPE applications or UF2 for PP or Nylon applications.
- Raise the heats up 20-30 f in the transfer line as well as in the die to ensure good flow
- Remove the machine off “Automatic” and into manual mode to avoid a pressure spike shutting down the extruder
- Slightly increase screw speed, making sure there is enough material flowing through the die
- Slow down take off roller speed to help ensure bubble remains intact
Ready to reduce your production downtime to protect your profits? Learn more about how purging compounds and process efficiency work in tandem.
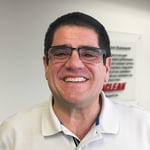
Eric Despotovich, an esteemed Asaclean Purging Expert and Technical Sales Representative, brings over 40 years of processing experience to his role. With over 18 years of dedication to our company, Eric has become a cornerstone of our sales team, renowned for his commitment to client success. His extensive industry knowledge and genuine passion for helping clients make him a trusted advisor in optimizing their operations. Eric's approach is characterized by deeply understanding each client's unique challenges, ensuring tailored solutions that drive efficiency and profitability.
Comments