In my experience I have seen several processors in the injection molding industry have issues with their valve gates. It is typical to see a build of colorant or degraded material hung up. What if I told you can manipulate these tools even further than just processing parts? Here are 5 quick steps to an open-mold procedure to use and tweak on your next problematic valve-gated tool changeover.
- Determine where the issue originates.
- Issues at the gate? – Manifold problems
- Issues on the part? – Material problems
- Clean the screw and barrel.
- High screw speed and back pressure are critical with a mechanical purge
- If it is a manifold problem? Is one gate more problematic than another?
- Increase heats in tooling – For carbon 550°F+ (290°C+)
- Isolate gates that are more of a problem – Shut the valves on the gates that are okay
- Increase injection pressure – More shear!
- Begin extruding material through tips or gates.
- Start at slow rpms to make sure you have flow
- Place something in front of B half of tooling – Cardboard is usually ideal
- Begin making short shots with the high injection speed and screw speed
- Open the rest of the gates and continue short high-velocity shots
- After the manifold is clean, do the following:
- Clean out the purge with high screw speed and back pressure from the barrel using production resin
- Open all the gates with a fresh sheet of cardboard in place. B
- Begin doing high velocity short shots until purge has gone away.
- Input parameters – start production!
Ready to reduce your production downtime to protect your profits? Learn more about how purging compounds and process efficiency work in tandem.
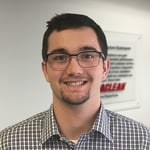
Jacob Puffer is a Technical Sales Representative at Asaclean-Sun Plastech, Inc. He started his career at Asahi Kasei Plastics of North America in Fowlerville, MI and attended Baker College of Flint.
Comments