I recently worked on a project with a plant manager at an injection molding plant in the Michigan area. He was making mouth guards in multiple colors out of a low-temperature thermoplastic elastomer (TPE). His dilemma was trying to figure out how to make quicker color changeovers.
He reported he was losing nearly thirty minutes and using approximately fifty-five pounds of polypropylene (PP) mixed with Tide laundry detergent per color change. He was going to be making these mouth guards in eleven different colors which translated to three dark to light color changes per week. What resonated the most was that this tool was only sampling stage and not even into production yet.
I spent some time with him examining the processing conditions to obtain a clearer understanding of why their process took so long, as well as consulting him on the best purge compound for his needs. The main driving factor considered was the TPE production processing temperature of 300F. The purge compound resolution not only had to clean well, but also, more importantly, it needed to easily clear out of the machine with the lighter color coming behind it.
Following the consultation, I recommended five tips:
- Use a low residue/temperature mechanical purging compound since it’s the best option for the production processing temperatures.
- Bump up the heat profile temperatures to somewhere slightly above 320F for purging.
- Use enough backpressure to keep the screw in the full forward position to clean the entire length of the screw from back to front (this also makes the volume the smallest).
- Use low to moderate screw RPM’s to ensure proper filling of the barrel and screw
- After correctly filling the barrel, use high screw RPM’s to force the purge into low-pressure areas so that it better attaches itself to the colorant.
After implementing my recommendations, the plant reported that the low-temperature purging compound worked great after a few trial runs with it. The color changeover process was improved. He spent just 5 minutes completing the color change, using around $5.50 worth of our E Grade. Saving roughly 83% on downtime for each color change will generate more machine capacity, especially once it goes into full production running on 10+ different colors.
Learn how to reduce machine downtime with five quick purging compound tips for your injection molding application.
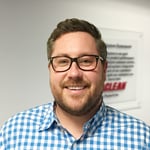
Ben Moore brings over 20 years of experience as a Purging Expert at Asaclean Purging Compounds, a leading manufacturer and distributor of purging compounds. As part of Asahi Kasei Plastics North America, Inc. (APNA), Ben has personally assisted hundreds of customers, helping them achieve significant cost savings. Based in Parsippany, NJ, Ben specializes in optimizing operations for thermoplastic injection molding, extrusion, compounding, and blow molding processes. His expertise lies in maximizing production efficiency by minimizing downtime and reducing scrap. For those interested in trying Asaclean products or seeking expert guidance, feel free to contact Ben directly. You can contact him at 800-787-4348, extension 227, or via email at bmoore@asaclean.com.
Comments