Contamination Causes Aren't Always Obvious
When dealing with contamination in plastic manufacturing, there are usual culprits we tend to look at: heat, residence time, layering, and challenging changeovers. While these factors can indeed cause contamination, leading to rejected parts, sometimes the root cause lies outside your process. Once you've ruled out these common suspects, consider the following unexpected sources of contamination:
1. Overhead Contaminants:
Dust and dirt can accumulate over time on the ceilings and surfaces above and below your machinery. Eventually, these particles fall into molds, boxes, or hoppers. Routine cleaning, either annually or biannually, can help mitigate this source of contamination.
2. Silos and Filters in Feed Systems:
These should also be cleaned regularly to prevent fine particles from accumulating and being fed into the machine.
3. Feeding Hoses and Ducts:
While these are usually not a problem if they're dedicated to a single resin, it's crucial to check for wear and tear, which could introduce metal contaminants. Make sure to replace temporary tape patches promptly, as debris can get stuck there.
4. Uncovered Boxes, Sacks, and Feed Hoppers:
These should be kept covered at all times to prevent contamination. Train your staff to value ground and waste or recycled material as much as virgin resin and to avoid discarding unrelated waste into these containers.
5. Fluid Leaks:
Water, oil, and other fluid leaks can cause contamination. Though not common, these issues can have a substantial impact, especially in thermoforming processes where they can multiply extensively.
5. Personnel and Robot Handling:
In many processes, parts are sensitive to touch. Employees should wear gloves to prevent leaving oily marks. Also, consider the potential for fabric lint from uniforms. Robot suction cups and grips should be made of materials that do not leave residues and can withstand heat.
Keeping these six contamination causes in mind will prepare you to address the root causes of your processing issues more effectively. Remember, Asaclean Purging Compounds can help remove contamination and lower scrap rates. However, you can prevent these self-inflicted wounds by addressing these external factors. These factors plague injection molders & extrusion converters alike.
Using the right tools and processes, you can overcome any processing challenges associated with difficult changeovers. Contact us today for a free consultation and ensure you get the most out of your process.
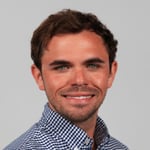
Tom Hanvey is the Product Manager for Sustainability for Asahi Kasei Plastics North America. Before joining APNA, he worked as the Senior Marketing Manager for Asaclean Purging Compounds. He's worked in the plastics industry for over 8 years and focuses on recyclable resins and on the inbound marketing side, providing easy-to-digest content to processors looking for an edge on their competition.
Comments