I’ve worked with numerous injection molding and extrusion plants over the course of my career since early 2000’s as a Technical Sales Representative. A question that comes up every now and then over the years from these processing plants is, “how should we reduce the overheating of a mechanical purge compound”?
Generally, this question pops up when the purge compound is used near or over the upper limit of its recommended operating temperature window and becomes over-sheared. I’ve fielded this question often enough to be able to propose some effortless fixes to try to alleviate this issue that your plant may or may not be aware of.
To reduce the overheating of a mechanical purge compound due to over-shearing, I’ve been suggesting 7 simple steps:
- 1.) Use the proper purge compound for the production resins
- 2.) Generally, it’s always best to purge at the normal operating temperature window of polymer
- 3.) Come off the back pressure slightly, while still using enough of it to keep the screw forward as much as possible
- 4.) Lower the screw RPM’s slightly, while still trying to maintain the high RPM’s
- 5.) Make sure your plant has proper ventilation at the machines since ANY resin in the market can emit gases when exposed to heat or too much of it
- 6.) Use Personal Protective Equipment such as a respirator
- 7)Empty the purge extrudate into a bucket of water
It should be noted that the overheating of any thermoplastic is possible. It’s not exclusive to just purge compounds.
These are straightforward and conventional suggestions that are generally painless and stress-free for the technicians. I recommend checking with your purge supplier to see if these small variations will work with their products while still generating a high level of purging performance.
Ready to reduce your production downtime to protect your profits? Learn more about how purging compounds and process efficiency work in tandem.
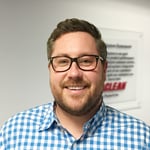
Ben Moore brings over 20 years of experience as a Purging Expert at Asaclean Purging Compounds, a leading manufacturer and distributor of purging compounds. As part of Asahi Kasei Plastics North America, Inc. (APNA), Ben has personally assisted hundreds of customers, helping them achieve significant cost savings. Based in Parsippany, NJ, Ben specializes in optimizing operations for thermoplastic injection molding, extrusion, compounding, and blow molding processes. His expertise lies in maximizing production efficiency by minimizing downtime and reducing scrap. For those interested in trying Asaclean products or seeking expert guidance, feel free to contact Ben directly. You can contact him at 800-787-4348, extension 227, or via email at bmoore@asaclean.com.
Comments