Learn Simple Ways To Effectively Clean Your Hot Runner Systems
Keeping the molding machine and hot runner clean and contamination-free is critical in the injection molding industry. Color and carbon contamination leads to defects, high scrap rates, and extended downtime.
The plastics processing community has largely embraced the use of commercial purging compounds and the implementation of proper purging procedures. However, many companies are still reluctant to put anything other than production resin through their hot runners.
Not all commercial purging compounds (CPCs) are suitable for purging hot runners. Before attempting to purge your hot runner system, check with your Asaclean Purging Expert to ensure the grade you're using is suitable for this task.
Many purging compound suppliers now make purging compounds specifically designed to clean hot runners. Although cleaning hot runners comes with challenges, the following tips will help make the process more efficient for your facility.
Challenges Of Cleaning Hot Runner Systems
Hot runner systems require extra care when compared with purging just a screw and barrel.
The relatively small clearance of the hot runner gate can present a challenge to clean due to purge viscosities, and any dead spot in the system is a potential sticking point for contamination as well as for the purging compound itself. Poor hot runner design leads to dead spots or low-flow areas where materials may hang up and burn. Since this happens in a low-flow area, it's often difficult to eliminate, even with a purging compound. Some high-cavitation hot runner molds are designed with ribs, cams, and undercut that make closed mold purging difficult, potentially minimizing the effects of the purging compound.
Sealing Your Machines At Shutdown
Hot runner systems often have multiple low- or zero-flow areas. Sealing your machines ensures that your purging compound displaces any heat-sensitive resin left from your last production.
Sealing your machines is typically done when shutting down for the weekend or before extended holidays. It prevents oxygen from entering your machines, which creates an environment where degradation and carbonization occur.
Purging Tips for Cleaning Your Hot Runners
To effectively clean your hot runner, follow these 8 purging tips:
- Check the gate clearance, and use a purging compound grade that clears the smallest system restriction.
- Use a purging compound that is compatible with the processing resin being molded.
- Check with your supplier before using glass-filled grades in hot runners or with highly-polished molds. Most of the time, glass-filled CPCs are not recommended for hot runners.
- Raise manifold heats only if doing so allows you to remain within safe operating temperatures. This allows you to dislodge the most stubborn deposits.
- If you observe color streaking or contamination in certain gate areas, close off all other gates. One at a time, inject high-velocity short shots through each affected gate to improve localized cleaning.
- When using the open mold method, perform short, high-velocity shots to promote turbulence within the hot runner.
- For extremely difficult purges with low-flow areas, try a chemical purging compound that can expand into dead spots and pull away the contamination that would otherwise be left behind.
- If possible, apply mold release to the cavities when purging the hot runner system with the closed mold method as you will be molding parts with the purging compound. These parts may not be fully formed, so the mold release aids in part removal.
When assessing your hot runner system, you must know the minimum clearances within the hot runner and at the gates. Also, it's important to understand if your hot runner has any poor design elements that may lead to low or stagnant plastic flow, as this affects what type of purging compound to use.
A high-quality purging compound should leave behind very little residue and remove carbonized resin or colorants, allowing for a quick return to production. Purging compound suppliers recommend different purging procedures for hot runners, and the method chosen depends on the resin(s) being processed, mold design, and cleaning difficulty. Always consult your supplier on proper purging procedures for your hot runner system.
Ready to reduce your production downtime to protect your profits? Request a Free Sample of Asaclean today.
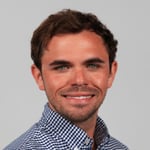
Tom Hanvey is the Product Manager for Sustainability for Asahi Kasei Plastics North America. Before joining APNA, he worked as the Senior Marketing Manager for Asaclean Purging Compounds. He's worked in the plastics industry for over 8 years and focuses on recyclable resins and on the inbound marketing side, providing easy-to-digest content to processors looking for an edge on their competition.
Comments