In 2 of my most recent blogs, I posed a few reasons why a strong purging program is a good idea and how to reduce costs (and headaches) on screw pulls at your injection molding or extrusion facility.
In today’s blog, it’s focuses on injection molding plants and their hot runners. With the assumption the leg work and research has been done upfront with choosing the best purging compound for the hot runner cleaning application, I’ve laid out 2 basic and broad views on how to effectively purge your hot runners:
This is straight-forward and self-explanatory. With the carriage up against and seated into the back of the mold while the mold plates are open, you can simply extrude the purge compound through the gates. Generally, this method better lends itself to larger parts with fewer drops/nozzles and generous gate tolerances. This method tracks and trends toward cleaning the manifold faster while using less purge compound overall for 2 reasons:
1.) You are not bound by the cycle time
2.) You are not molding parts so usually less purge compound is required.
I think it’s worth mentioning that if your tooling happens to be equipped with valve-gates, you have an option where you can close the valve pins for a few moments to generate pressure in gates and open them back up to provide pressure relief. Furthermore, if your tooling is valve-gated and you can individually open/close them, you can isolate your problematic & non-problematic gates.
2.) Closed Mold Method
Again, pretty straight-forward and self-explanatory, but tends to be slightly trickier compared to open mold method. Just what you would think…you are molding and cycling through full (or partial) parts with purge compound while cleaning. Generally, this method better lends itself to smaller parts with more drops/nozzles, higher-cavitation tools and tighter gate tolerances.
This method tracks and trends toward cleaning the manifold a little slower while using more purge compound overall for the opposite reasons mentioned above. However, more pressure is generated by molding parts so usually that enhances for cleaning abilities.
If molding parts is the best option, we recommended 3 tips:
1.) Reduce cooling time along with a healthy dosage of mold release sprayed to the cavities (reduces the likelihood of parts getting stuck in the cavities)
2.) Remove pack and hold pressures along with velocities
3.) If possible, short shot the parts when injecting and molding the purge compound (use enough of shot so that the parts remove from cavities).
As with most things in life, each of these methods comes with pros and cons. Take them with a grain of salt, as every tool and manifold come’s with its own personality. My best suggestion would be to work with your purge supplier and have them guide you to the best solution that should be used.
Are you curious about mastering the basics of hot runner cleaning with purging compounds and leveling up your purging program? If you are interested in learning more, schedule a free 10 minutes consultation today.
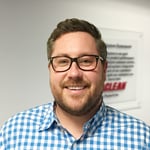
Ben Moore brings over 20 years of experience as a Purging Expert at Asaclean Purging Compounds, a leading manufacturer and distributor of purging compounds. As part of Asahi Kasei Plastics North America, Inc. (APNA), Ben has personally assisted hundreds of customers, helping them achieve significant cost savings. Based in Parsippany, NJ, Ben specializes in optimizing operations for thermoplastic injection molding, extrusion, compounding, and blow molding processes. His expertise lies in maximizing production efficiency by minimizing downtime and reducing scrap. For those interested in trying Asaclean products or seeking expert guidance, feel free to contact Ben directly. You can contact him at 800-787-4348, extension 227, or via email at bmoore@asaclean.com.
Comments