We are familiar with the two extrusion blow molding die-head types: accumulator (or intermittent) and continuous. While each type has advantages depending on the size and complexity of the part, resin type, required cycle times, and other factors, one of (if not the greatest) differences between the types is how difficult a purging event can be.
Overall, extrusion blow molding is a lower-pressure process than injection molding, leaving us with very few machine parameters to assist a purge product, whether mechanical or chemical purge type. Continuous extrusion die-head types are pretty straightforward, containing chambers and material flow routes that don’t typically bring many “hang up” spots such as low flow / low-pressure areas. Usually, the feed blocks or distributor zones right before the head bring greater purging challenges. Still, the head is relatively easier to purge when removing resin for color/material changes or for carbon contamination. On the other hand, accumulator die-head types bring a specific challenge: how to deal with the hang-up spots in the piston chamber.
The most significant difference in the hardware is the piston that moves vertically inside the head’s chamber, moving downward from a set point (shot size) to create the appropriate sized parison. The upper part of the chamber, between the piston and walls, is where material hangs up the most, caused by the piston’s upward movement while dosing the shot. Many of these heads have “weep holes” near the top, allowing degraded plastic to exit the head via these ports. A shot-size “line” becomes prominent inside the head during longer runs. During a recent trial, we worked with the operator to define which set point(s) would tend to show the most contamination from previous colors or carbonized/degraded material hung up in the upper parts of the chamber, or other words, finding that “line” where hang up sticks. In this case, they would run a smaller part at 16% with no problems and a larger part at 30% with no issues. However, when the set point/shot size was 65% or larger, the material coming out would often be laden with older colors from previous runs and even specks or chunks of carbon contamination. We concluded the “line” is approximately 65% shot size.
This knowledge of scrap history helped us define the best procedure for purging. For this application, a chemical purge was preferable over a mechanical (scrubbing) purge grade due to its gassing and expanding properties to better access the hang-up spots that a mechanical purge would take far too long to get to. For purging, we decided to fill the head at an approx. 80% set point and only shooting about 30% down, restricting the piston positions to only between 80 and 50%. This accomplished two things:
- Raising the set point above the targeted 65% “line” allowed the purge to access the contamination from the top down.
- Allowing the chemical reaction to clean from above the area.
- Showing the evidence of hang-up.
Secondly, performing repeated shorter shot sizes with only a net 30% change in piston position consumed far less purge instead of displacing the entire 80% repeatedly. The color lines were removed in 80 minutes, drastically improving their typical 8 to 10 hours lost when purging with resin.
The main takeaways here: for purging, change the set point to a higher position than the minimum point where contamination shows up, and only perform short shots while keeping the head relatively full, avoiding full head displacement shots to save on purge quantity.
Ready to get your production team well-trained and implement a comprehensive purge training program?
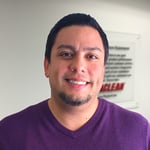
Celebrating his 24th year with Asaclean - Asahi Kasei Plastics North America, Lenny Gutierrez is a renowned purging expert who played a pivotal role in the company's expansion into Mexico in 2009. Currently, he excels as a Technical Sales Representative for Ohio, Illinois, and Missouri, combining his extensive industry knowledge with a strategic approach to drive sales and client relations. Lenny is also a prominent presenter at tradeshows and conferences, representing Asaclean with his expertise and professionalism.
Comments