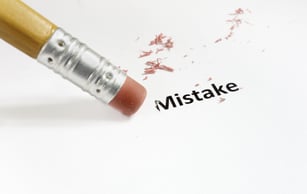
The purging procedures and compounds you use have far-reaching financial impacts that extend well beyond cost per pound. Too often, plastics processors fail to use the appropriate purging compounds or don’t implement proper purging procedures. Each of these issues hurts your profitability and efficiency.
Here are three common mistakes to avoid when using a purging compound:
1. Using A Cheaper Virgin Resin Or Regrind To Purge
In an effort to save money, some plastics processing manufacturers turn to a cheaper, lower-quality virgin resin to address their purge problems. However, this tends to make purging problems even worse.
“Old-school” purging methods — such as flushing the machine with the next resin or regrind — are time-consuming, material-wasting and ineffective at removing color and carbon contamination. These materials are not designed to clean machines. When using regrind or virgin resins to purge, the material simply creates another layer over any existing resin layers, color deposits and carbonized material within the barrel.
2. Selecting A Purging Compound Based On The Wrong Criteria
The following are a few examples of how you might be selecting (and evaluating) a purging compound based on the wrong set of standards:
- Determining a purging compound’s overall value based on price-per-pound alone.
- Not knowing your current total purging costs before evaluating the impact of a commercial purging compound on total purging costs.
- Failing to consider other critical purging factors, such as scrap rates, machine downtime, the amount of purge needed for an effective clean, and the amount of replacement resin needed to remove purge from the machine. Think along the lines of good part-to-good part.
3. Not Following The Supplier’s Recommended Purging Procedures
This cannot be stressed enough: You must document specific instructions to share with anyone who is involved in your purging procedures.
You’d be surprised how many facilities don’t have documented purging processes at machines and don’t monitor their purging processes.
It’s important to lean on your purging compound representative for advice. Don’t expect great results if you lack consistency in purging practices from person to person and shift to shift. Not following the manufacturer’s product instructions often leads to costly mistakes.
Taking shortcuts with your purging procedures or using cheaper purging alternatives often leads to lost profitability and increased machine downtime. To improve efficiency and get the most out of your purging process, it’s essential that you use the right purging compound, implement proper purging procedures and follow recommendations from your supplier.
Learn how the right purging compounds and procedures impact your process efficiency.
Comments