Ever notice those pesky black specks or streaks marring your blow molded parts? You're not alone. Carbon lumps and degraded resin are common foes, leading to production headaches – rejected parts, wasted time, and lost profits.
If you work in maintenance or production and this scenario sounds familiar, this blog can help prevent these episodes.
It might be assumed that a myriad of variables causes the problem, the main ones being:
- Machine errors preventing the correct temperature control of various zones
- Resin contamination
- Bad resin batch
While the above can be part of the problem, some variables are not necessarily the sole reason, and ruling each out takes time and resources. The worst part is having to disassemble the machine, remove the screw, and still not finding the root cause of the problem, causing the episode to repeat over and over.
In extrusion blow molding, various configurations for forming the parison exist; these configurations all have points or zones with different pressures and flow rates in common. These low-pressure and low-flow areas of plasticized resin lead to the appearance of carbon lumps and degraded resin. The cause of these lumps is related to residence time, and the layers of degradation that come off at any time cause contamination to appear randomly during production. That's right, not necessarily due to the startup but because of the accumulation of previous events.
With the implementation of an appropriate purging program that includes a suitable compound and best practices, an optimal preventive approach can be achieved in cases such as:
This eliminates the appearance of these lumps during startup and production, avoiding the costs associated with downtime, part rejections, and maintenance interventions on the equipment.
One option is a purge concentrate like Asaclean PLUS grade. Its action method helps displace these lumps in low-pressure and flow areas, preventing the formation of carbon deposits and allowing the equipment to be sealed.
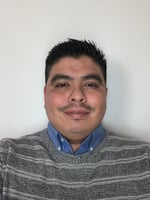
Lazaro Estrada, a skilled Technical Sales Representative for Mexico at Asahi Kasei, has a distinguished engineering and process optimization background. Before joining Asahi Kasei, he was instrumental in developing projects with clients for the selection and implementation of injection and die-casting machinery, including overseeing their installation and startup of new processes. Holding a professional degree in Electronics with a specialization in automation, Lazaro's career has been defined by his leadership in project development, ranging from chemical industry reactors and synthesis to machinery and continuous improvement in the plastic industry. His expertise and forward-thinking approach make him a key resource for clients aiming to advance their operational capabilities.
Comments