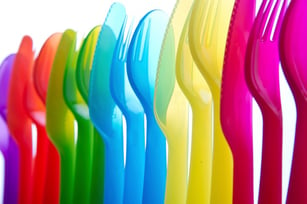
Taking a reactive approach to your purging process is not the way to increase the effectiveness of your purging compounds. Being proactive by using purging compounds on a regular basis and training your employees on proper purging procedures goes a long way in helping you maximize your bottom line.
The following are three common mistakes that plastic processing companies make in an attempt to save time and money. Unfortunately, these efforts often negatively impact your purging process.
Purging Mistake #1:
Taking purging shortcuts to save time.
Sometimes operators take shortcuts by using the “auto-purge” functionality while purging injection molding machines.
The problem with auto-purge is that the default speeds and pressures aren’t usually what purging compound suppliers recommend. Generally speaking, if you’re using a mechanical purging compound, you want to purge with the highest pressures and speeds that you can safely run. You also want to keep the screw in the forward position while purging.
Auto-purge is rarely set up with any of these conditions maximized, and it leads to overuse of the purging compound because the purge is rendered less effective.
Purging Process Tip: To minimize your purging expenses, make sure your molders or technicians are purging manually under the recommended conditions.
Purging Mistake #2:
Not using enough purging compound in an attempt to save money.
Insufficient purging during downtime and changeovers – that is, not using enough purging compound – may increase scrap rates.
Avoid using a predetermined amount for every purge. Some companies weigh out “X” number of pounds and tell the operator, “This is the amount you will need to purge.”
However, different processing parameters and materials may require different purging agents and/or procedures. For instance, the longer it’s been since a screw pull and full cleaning, the more contamination you will have in your system, requiring more purging compound.
This is especially true in extrusion, where carbon accumulates in low-pressure areas like dies, die heads and blow molding accumulator heads. The purge must be carefully inspected during purging to understand when the machine is sufficiently purged.
Purging Process Tip: Train your operator to purge as long as necessary, within a certain tolerance range. Simply putting the machine back into production after purging “X” number of pounds isn’t the right approach.
Purging Mistake #3:
Failing to fully clean the screw manually.It’s critical for processors using purging compounds to understand that a full manual cleaning of the screw may still be necessary at some point. If screws, barrels, nozzles, dies or die heads have not been cleaned in a long time, a purging compound may not be enough.
Purging Process Tip: Purging compounds work best when used as a preventive measure, as opposed to a reactive measure. Check for process and part consistency. If you observe extreme contamination, clean everything manually, and then start a regular purge program.
If you’re dealing with slow color/resin changeovers, too much contamination and high scrap rates, it’s likely you’re making one of these three purging mistakes. Properly training your employees can help prevent these mistakes and lead to more efficient production runs.
Learn how insufficient purging training is costing you in dollars and downtime.
Comments