Burn marks appearing on injection molded parts is one of the most common defects molders have to deal with from a quality standpoint. They can show up at any time during the molding process and determining quickly the root cause is extremely important in reducing machine downtime and product loss due to quality concerns.
I will highlight some causes stemming from three different areas which are machine, mold, and material and give some suggested remedies to help deal with this common defect.
Machine: Several different things can cause burn marks associated with the machine or the process. The material could simply be too hot in which case the melt temperature should be reduced. Burns can also be caused by the mold being filled too quickly and you would need to reduce the injection speed. If the back pressure is too high that can also cause burn marks. Improper purging of the previous resin can show up as burns in the current run where the previous material was left to cook in the barrel causing burnt material to hinder the current run. A proper purging procedure should always be put into place when changing materials or performing color changes.
Mold: If the mold is not properly vented or the clamping pressure is too high then air trapped in the cavity can cause the edge of the part to burn where the improper venting is taking place. In this case, the mold should be inspected and the venting fixed to where proper gas release can be accomplished when molding.
Material: If the material or resin being ran is wet or has excessive moisture content, then that can cause burn marks to be present in the finished product. If this is the case, the molder should look at drying the material to proper specs before continuing molding applications.
Ready to reduce your production downtime to protect your profits? Learn more about how purging compounds and process efficiency work in tandem.
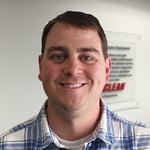
Jeremy Cooley is an Asaclean Technical Service Representative & Purging Expert living in South Carolina. He's worked in injection molding & purging for over 15 years, and frequently presents at national plastics trade shows and conferences.
Comments