Processing Super-Engineering Resins like PEEK, PEKK, ULTEM, Torlon, PSU or Teflon can be very difficult. Once you get up into the 700°F range or above, things can get tricky. Starting up these runs can be what I call "white knuckle driving. They need a watchful eye, immediate attention and quick thinking. If things go wrong, they go wrong very quickly and in a bad way. This leads to lots of very expensive scrap and down time.
Non-Purge solutions are often also very expensive and timely involving things like screw pulls and replacing components of equipment. Without the right purge, your problems can compound (no pun intended).
Now that you got that material into your system, how do you get it out safely, effectively and completely? What happens if your running one of these high-temp materials and you need to change to a regular commodity resin? How do you effectively purge the machine and bridge the temperature gap from one to the other? These types of changeovers happen every day for injection molders and especially custom molders. The schedule can’t always be perfect. Molds are always running in different machines. You must know what to do--just be prepared and just roll with the punches.
When it comes to purging these materials out safely, effectively, and completely for production color or material changeovers and weekend shutdowns, we have some good options.
This is not meant to be a product plug, but in my years as a molder, I never found products that worked better for super-engineering resins than Asaclean PF & PX2 Grades. They are what I used before I joined Asaclean, and I believe in the products.
These are specifically designed for High-Temperature purging from 535°f(280°c) up to 790°f(420°c). They are extremely effective in managing the high heat demand of these super-engineering materials. This enables them to safely and effectively clean and displace your high heat materials.
If you are scheduled to perform a color change on a super-engineered material or a material change from one on high heat material to the next, you can use either the PF or PX2 to quickly transition for one to the next reducing time and scrap. The PX2 will give you added scrubbing if needed.
If you are planning on shutting the machine down for the weekend and are going to resume production with the same high heat material the PF Grade can be used to safely shut down and seal the barrel for a faster and cleaner start up on Monday morning. If you are planning to perform a material change over to a much lower processing melt temperature material below 535°f, this will undoubtedly need to be a two-step process in order to properly purge the super-engineered material and then remove the high temperature purging compound from the system as well.
In order to transition temperatures below the 535°f threshold you would use our EX Grade at 550°f. Following our purging procedure, the EX will quickly and completely remove all remaining PF or PX2 high temperature purging compound and any remaining contamination in the barrel or on the screw allowing you the flexibility to reduce your barrel temperature and transition you to your next lower melt processing temp material all the way down to 390° if necessary.
Super-engineering materials are very expensive and when you run into trouble it is surprising how quickly the material scrap cost can add up. Being prepared with the proper purging compounds and procedures can help mitigate the damages and get you back running production as quickly as possible.
Let us know if you'd like a free consultation or free on-site support.
Ready to reduce your production downtime to protect your profits? Learn more about how purging compounds and process efficiency work in tandem.
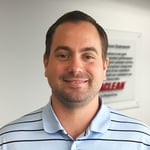
Hank Moeller is an Injection Molding and Purging Expert with over 20 years of experience in a processing environment.
Comments