Cleaning hot runner manifolds, especially when they have never been cleaned before, can be a daunting challenge for injection molders. I recently had the opportunity to assist a major Injection Molding company struggling with its production line. Their highest-producing part was molded using UL FR-ABS material, which, unfortunately, was not very profitable due to significant amounts of scrap, press downtime, and costly monthly tooling overhauls.
Historically, the company has tried various purging compounds with limited success. When I arrived, I introduced a mechanical purging compound, expecting it to perform better than previous attempts. After running 50 pounds through a 1500-ton press to clean the barrel and screw and then molding parts through the hot runner tool, I was surprised to see minimal contamination removal.
Fortunately, I had a backup plan with our new PLUS grade concentrated purging compound, a heat-activated solution. We prepared a 20% mixture of 100 pounds of purge compound blended with their standard natural ABS material. By raising the hot runner manifold temperatures by 50°F above the normal set-point and purging again immediately after using the mechanical option, we began to see results. First, we flushed out the initial purging compound from the barrel, followed by the stationary manifold on the A-side.
After initiating a cycle of molding parts with the heat-activated concentrate mixture, we set the press to semi-auto mode and allowed the manifold to soak for five minutes, letting the purge work to break down and loosen contamination. Following the soak period, when we resumed the cycle, the molded parts emerged covered in a dark brown, mud-like contamination—indicating we were on the right track.
We repeated this cycle—molding five shots and then allowing a five-minute soak—until the entire 100-pound batch was used. This approach proved that our heat-activated purging option was far superior for cleaning the manifold than the mechanical alternatives. The 20% mixture facilitated molding parts with minimal parameter adjustments and allowed the concentrate to build pressure in low-flow areas and effectively loosen all contamination for removal.
Since adopting our PLUS grade concentrated purging compound, the company has not only eliminated the need for costly manual cleanings and acid baths but has also witnessed a significant reduction in scrap. This shift has resulted in markedly improved profitability and decreased lead times, demonstrating the tangible benefits of our advanced cleaning solution. We are committed to ongoing partnerships with our clients, providing continuous support and training to ensure they achieve the best possible outcomes with our products. Together, we are setting new standards for efficiency and quality in the injection molding industry.
Ready to reduce your production downtime to protect your profits? Learn more about how purging compounds and process efficiency work in tandem
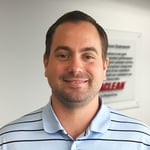
Hank Moeller is an Injection Molding and Purging Expert with over 20 years of experience in a processing environment.
Comments