The shutdown process is as critical as the operational phase in plastic processing. Whether it's injection molding, extrusion, or blow molding, shutting down your machinery can significantly impact your next production run. One common issue plagues many processors is the appearance of black specks at the start of a new run. This blog delves into the root cause of these contaminants and how a strategic approach to machine shutdown can prevent them, ensuring a pristine start every time.
Understanding the Cause of Black Specks
The black specks that mar the quality of plastic products originate from the residue left in the machine's barrel after a shutdown. Traditional shutdown procedures often involve running the machine until the barrel is empty and then turning off the heat. However, this method leaves behind production material, oxygen, and residual heat—a combination that fosters the degradation of leftover material and the formation of carbon specks.
The Role of Purge Compounds in Shutdowns
To address this issue, implementing a purge compound designed explicitly for shutdowns offers a game-changing solution. Purge compounds, particularly thermally stable ones, act as a sealant within the barrel. This practice eliminates the residue that leads to contamination, minimizes oxygen exposure, and utilizes the residual heat in a manner that doesn't compromise the integrity of the next production run. Asaclean's range of purging compounds, for example, provides a variety of formulations tailored to meet different machine shutdown needs, ensuring that processors can start their operations without the setback of black specks.
The Benefits of Sealing with Purge Compounds
By adopting a purge compound as a standard part of your shutdown protocol, you stand to gain several benefits:
- Reduced Contamination: A clean barrel means a clean start. Eliminating residues significantly lowers the risk of contamination, leading to fewer rejects and higher-quality products.
- Cost Savings: Minimizing the formation of black specks reduces waste and the need for reworks, translating into direct cost savings and more efficient material use.
- Increased Operational Efficiency: A clean start means less downtime and fewer interruptions for cleaning and maintenance, maximizing operational efficiency and productivity.
Tailoring Your Shutdown Procedure
It's important to recognize that not all production materials are suitable for sealant use due to their thermal stability. Selecting the right purge compound for your shutdown and sealing process is crucial. Asaclean offers a variety of grades to match different processing requirements and materials, ensuring that your machine is ready for a contaminant-free start.
Conclusion
Effective machine shutdowns are critical to maintaining high standards in plastic processing. Integrating thermally stable purge compounds into your shutdown routine can prevent the formation of black specks, enhance product quality, and streamline your operations. For any queries or further assistance in selecting the appropriate purge compound, our team is always here to help at edespo@asaclean.com.
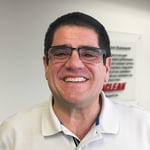
Eric Despotovich, an esteemed Asaclean Purging Expert and Technical Sales Representative, brings over 40 years of processing experience to his role. With over 18 years of dedication to our company, Eric has become a cornerstone of our sales team, renowned for his commitment to client success. His extensive industry knowledge and genuine passion for helping clients make him a trusted advisor in optimizing their operations. Eric's approach is characterized by deeply understanding each client's unique challenges, ensuring tailored solutions that drive efficiency and profitability.
Comments