To paraphrase Thomas Edison when asked how it felt to fail at making a light bulb over 1000 times, he stated, “I didn’t fail over 1000 times, I learned over 1000 ways how not to make a light bulb.”
Many plastic processors experience the same thing. I’ve been working with a blown film manufacturer that’s been forced to use post-consumer recycled plastic (PCR) due to state mandates. In the past the requirement was 20% and has been increased to 40% as of April 1, 2020.Running PCR’s has its inherent problems. The spec range on the products vary widely. Even in best conditions PCR’s will degrade more quickly than a prime resin over time causing die lines, carbon specks, scrap and collapsed bubbles.
Blown film processors running PCR’s will try every trick in the book to minimize the contamination build up and after numerous attempts eventually have to manually tear down and clean the machine which takes several hours and sometimes even days. We’ve learned that all the countless previous attempts / solutions only wasted time and money. A proactive approach is what’s called for.
When it come to the point where a manual tear down and clean is necessary, take the time and effort to complete it as thoroughly as possible. That includes cleaning the extruder(s), downstream plumbing, melt pumps, static mixers if any and the die. Take the time and do it right…. It will save you in the long run.
Once the system is clean, resume production. At the very first signs of contamination use a good purge compound to remove the buildup. PCR’s will degrade quickly. The object is to catch it early enough where a commercial purge has a chance to remove the contamination. In cases where your running a 40% blend of PCR’s, you will be purging more frequently but that beats the alternative. Preventative Maintenance purging has proven to be the best solution.
Ready to reduce your production downtime to protect your profits? Learn more about how purging compounds and process efficiency work in tandem.
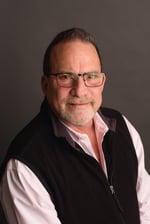
Chris Melchiore, serving as Business Development Manager at Asaclean Purging Compounds, excels with his specialized knowledge in Chemical Purging Compounds and Concentrate Grades. His industry journey, extending over two decades, includes a notable 16-year stint at NOVACHEM before joining Asaclean in 2015. Beyond his core role, Chris is actively involved in speaking engagements at webinars and tradeshows, showcasing his expertise and contributing to the broader industry dialogue. His insights and experience make him a pivotal figure in both business development and educational outreach for Asaclean.
Comments