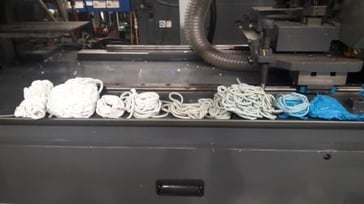
Do you have a difficult color change that takes too long to clear up?
Don’t just purge the screw and barrel. Focus on areas that commonly cause color and contamination issues.
1-Nozzle Body and Tip
The nozzle body and tip is a dead spot for material. Even when the screw and barrel have been emptied and the screw is in the full forward position, there is usually a small amount of material stuck here. This often leads to a layer of degraded material on the inner wall of the nozzle body. This shows up as off color streaks or specks in the molded part in the first area of the cavity to fill out. To address this, raise the set-point of the nozzle zone 50-75°F at the start of the color change. The additional heat will help to break up the degraded layer and be displaced during the purging process. Return the nozzle to normal set-point when the new color/material is introduced into the screw and barrel.
2-Feed-Throat
The feed-throat can be a source of contamination. There are often hang-ups here. Look for steps and ledges at magnet boxes, hoppers or blenders. These areas can hide stray pellets that trickle into the material stream. Be sure to address these areas when cleaning out the hopper and loading system. A few pellets of colorant can result in the scrapping of dozens of parts.
3-Check Ring
Another potential problem area is the check ring. When purging, alternate short, fast, air shots with long decompression stokes to force material through the check ring assembly. This will help clear out any stubborn color that can linger here.
Addressing these problem areas early in the process will result in faster, more effective “good part to good part” color changes.
Discover more ways to reduce thermoplastic molding scrap.
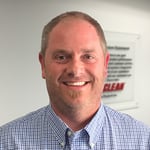
With over 30 years in the field, Jerry Weddell is a Technical Sales Representative with a wealth of knowledge in mold-making and purging compounds. While his expertise spans injection molding, extrusion, and blow molding, he is particularly distinguished in injection molding. Jerry's profound understanding of these processes enables him to offer targeted, practical solutions, especially in the nuanced aspects of injection molding. His commitment to providing exceptional guidance and support to clients has made him a respected and trusted figure in the industry.
Comments