Manufacturers in sheet extrusion face numerous challenges. In the heart of Virginia, a prominent manufacturer of lightweight roofing sheets and panels sought to optimize their sheet extrusion process. They faced constant contamination issues in rigid PVC and polycarbonate extrusion. This article takes you through their transformation journey, highlighting how I was able to help them find the best solution for their particular needs. Our customized purge program outperformed rival options, leading to significant efficiency gains in the extrusion process. But let's go back to the beginning.
The Contamination Challenge in Sheet Extrusion with PVC & Polycarbonate
The process of sheet extrusion and PVC processing has its unique hurdles. Manufacturers working with rigid PVC and polycarbonate have to contend with the distinctive characteristic of these materials being highly susceptible to residue buildup on essential equipment such as the screw, barrel, and die edges. This buildup doesn't just lead to carbon contamination; it has a domino effect, compromising product quality and resulting in undesirable consequences such as lengthy downtime, increased material waste, and frequent, often costly, equipment maintenance.
Their Game-Changer in Contamination Management
As industry leaders, the Virginia-based sheet extruder recognized these challenges and understood the necessity for a high-performance purging compound. Their goal was clear: to find an effective solution that would not only remove PVC residue but also prevent carbon contamination. They needed a purging compound that stood head and shoulders above the rest, one that would outperform other competitors in the extrusion purging compound market. Their search led them to Asaclean.
I immediately visited their production site to assess the situation and design a purge program tailored to their needs. After a series of tests on various alternatives, the results were clear. Asaclean's C Grade emerged as the most effective solution, outclassing all other compounds they had trialed. The manufacturer was pleased with the results, which included a significant decrease in contamination, downtime, and material waste.
The Asaclean® Advantage: Increased Efficiency and Cost Reduction
Embracing Asaclean's C Grade purging compound led to dramatic improvements in the manufacturing process. The case study results painted a compelling picture of the effectiveness of our purge program:
1. Dramatic Decrease in Purge Material Usage
Before implementing Asaclean C Grade, the company used an average of 80 lbs. of in-house purge material. This quantity dramatically decreased to 20-25 lbs. of Asaclean C Grade.
2. Eliminate Costly Downtime
Time is money in manufacturing. The typical downtime associated with the in-house purge process, which was around 2 hours, was reduced to approximately just 1 hour using Asaclean C Grade.
3. Reduce Scrapped Parts & Waste
The number of scrapped panels decreased from an average of 80 to just 12-15. This reduction resulted in considerable cost savings.
The results were unmistakable. By partnering with Asaclean, the Virginia-based sheet extruder overcame contamination challenges and significantly streamlined its production process. Asaclean's C Grade proved to be an efficient and cost-effective solution, guaranteeing the consistently high quality of their lightweight roofing sheets and panels while outshining other extrusion-purging compounds on the market.
The Right Choice for this Process
By choosing Asaclean C Grade purging compound, the Virginia-based sheet extruder discovered the ideal antidote to their challenges. The benefits were immediate and substantial; Asaclean C Grade allowed them to uphold superior product quality, minimize downtime, and significantly cut production costs.
However, it's not only the tangible benefits that set Asaclean apart. The company's dedication to delivering exceptional customer service was another critical component of this success story. With their deep understanding of the industry and customer needs, Asaclean was able to offer a tailor-made solution that fit the manufacturer's specific requirements like a glove. This commitment to client success goes beyond merely providing a product; it's about walking the journey with the client, ensuring they overcome their production challenges and reach their efficiency goals.
Conclusion
Moreover, Asaclean C Grade's versatility also significantly influenced its adoption. Suitable for various applications, this purging compound excels in preventative cleaning, color changes, carbon removal, and shutdowns. Its versatility means it's not just a solution for a single problem but a tool to improve overall operational efficiency.
Another critical aspect to consider is sustainability. Asaclean C Grade helped improve operational efficiency and contributed to the manufacturer's sustainability efforts by reducing waste. In the face of increasing environmental concerns and stringent regulations, choosing a solution that aligns with sustainability goals is a win-win.
Asaclean's C Grade has proven to be a transformative solution, enabling the Virginia-based manufacturer to maintain the high quality of their lightweight roofing sheets and panels while surpassing other extrusion-purging compounds. Yet, this is just one of many success stories. Asaclean's purging compounds serve various industries, helping numerous businesses optimize their processes, reduce costs, and increase efficiency.
Ready to reduce your production downtime to protect your profits? Request a Free Sample of Asaclean today.
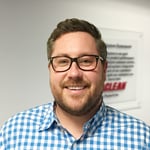
Ben Moore brings over 20 years of experience as a Purging Expert at Asaclean Purging Compounds, a leading manufacturer and distributor of purging compounds. As part of Asahi Kasei Plastics North America, Inc. (APNA), Ben has personally assisted hundreds of customers, helping them achieve significant cost savings. Based in Parsippany, NJ, Ben specializes in optimizing operations for thermoplastic injection molding, extrusion, compounding, and blow molding processes. His expertise lies in maximizing production efficiency by minimizing downtime and reducing scrap. For those interested in trying Asaclean products or seeking expert guidance, feel free to contact Ben directly. You can contact him at 800-787-4348, extension 227, or via email at bmoore@asaclean.com.
Comments