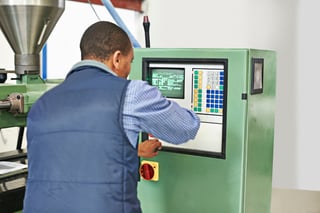
You may think you know what your melt temperature is, but do you really? Do you know what the barrel temperature set-points are on your injection molding machine? Do you think these are the same? They’re not.
Let’s assume that all the thermocouples, controllers, and heater bands are working in perfect harmony. Now are they the same? It's highly unlikely.
Several things can influence the melt temperature on a molding press. Back pressure plays a large part. Screw design also plays a large part. Material type, residence time and equipment wear all contribute as well. Are you using a lot of back pressure or a little? Do you have a general-purpose screw or a mixing screw? What does general purpose really mean? What is the material’s residence time = How many shots are in the barrel?
The point is that many things contribute to the temperature reached by the plastic melt during a production run. How do you really know where you are? A melt temperature probe can solve this issue and make sure you're getting better, more consistent parts.
I am surprised how many molders do not have this basic piece of equipment. It is the only reliable way to know how hot it really is. If you have a new mold you’re shooting for the first time, verify and document the melt temperature. Collect some data so you can establish a baseline. If you find yourself having a really good run on a difficult job, check the melt. If your part is not running as well as it normally does, check the melt. Collect some data. If you want to start a preventative maintenance program, check the melt & collect some data. These two steps are very beneficial in any situation.
Learn about the importance of implementing proper purging procedures by downloading this free industry guide.
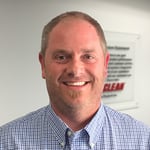
With over 30 years in the field, Jerry Weddell is a Technical Sales Representative with a wealth of knowledge in mold-making and purging compounds. While his expertise spans injection molding, extrusion, and blow molding, he is particularly distinguished in injection molding. Jerry's profound understanding of these processes enables him to offer targeted, practical solutions, especially in the nuanced aspects of injection molding. His commitment to providing exceptional guidance and support to clients has made him a respected and trusted figure in the industry.
Comments