An often overlooked part of the injection molding process is the nozzle tip. The nozzle tip is the point where the molten plastic leaves the injection unit and enters the mold.
The interface of the sprue bushing of the mold and the nozzle tip of the injection unit is intended to help insure the two are properly aligned. Severe misalignment can result in damage to the nozzle tip and/or sprue bushing, as well as leaking of plastic during injection. Proper alignment also allows for plastic to be injected into the mold with a clear path into the runner system. A properly selected, and properly aligned nozzle tip should allow for a robust processing window.
What size is yours? ½” radius?, ¾”? Full flow, reverse taper? There are many styles. How do you decide which one is right for you? Match the radius of the sprue bushing on the mold. The most common sizes are ½ and ¾”. 0.5 or 0.75” if you prefer. Next, verify the size of the sprue bushing orifice. The nozzle tip opening should be just smaller than the sprue bushing orifice. If the sprue is ¼”, the tip should be 3/16”. If the sprue is 3/8”, the tip should be 5/16”. Just smaller, never larger.
A nozzle tip that is larger than the sprue bushing can cause several processing issues.
- Runner sticking in mold. The mismatch at the tip orifice can cause flash that makes it difficult for the runner to pull.
- Color streaks or splay. When the sprue orifice is smaller than the nozzle orifice there is a lip around the opening protruding into the melt stream. This can cause shear that shows up on the molded parts as splay or color streaks.
A nozzle tip that is much smaller than the sprue bushing orifice also causes issues. The smaller the tip orifice the more pressure needed to overcome the restriction. The greater the pressure drop across the tip, the more of an influence it can have on the process. Pressure Drop=Smaller Process Window.
A nozzle tip that has a mismatched radius with the sprue bushing can cause several processing issues.
- The most obvious and most costly issue is leaks. An unnoticed nozzle leak can very quickly get into heater bands and thermocouples. This will result in very costly replacements cost as well as unplanned downtime.
- Short shots. The intermittent leak of plastic didn’t go where you wanted it to. Will your operator catch the defect?
- A mis-matched or damaged nozzle tip can allow air to enter the melt stream during injection. This can show up on the parts as splay.
Something that seems as simple as a nozzle tip can have a big impact on your process. Standardize if you can. At least get down to one radius, and pay attention to the orifice.
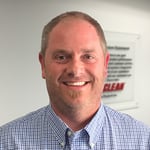
With over 30 years in the field, Jerry Weddell is a Technical Sales Representative with a wealth of knowledge in mold-making and purging compounds. While his expertise spans injection molding, extrusion, and blow molding, he is particularly distinguished in injection molding. Jerry's profound understanding of these processes enables him to offer targeted, practical solutions, especially in the nuanced aspects of injection molding. His commitment to providing exceptional guidance and support to clients has made him a respected and trusted figure in the industry.
Comments