A production team producing plastics typically is made up of various experts that work together and a level of trust is built among the team members. Have an issue with a hot runner not working properly? Machine not running as expected? Production planning now needs to accommodate new customers or last-minute JIT jobs? Part quality and inspection need to add a new spec to acceptable part criteria? There’s a person or department in charge of every aspect of a production run and to state the obvious, communication is of the utmost importance. Reach out to the expert, he or she will know what to do.
The role of a purge supplier varies greatly depending on the level of involvement allowed by the plastics processor. Many times at the start of the relationship with a purge supplier, a production house reaches out to solve a singular or pressing issue that needs to be resolved in a timely manner. The purge supplier recommends the correct product, trains the end user, and boom, the issue is resolved. This was only possible because the company deferred to the supplier to obtain “purge product expertise”. On the other hand, you would be hard-pressed to find a process engineer that doesn’t already have their own perspective and methods on how to purge a machine or what process changes to apply when trying to define how to fight contamination issues. Many production team members bring a wealth of experience and knowledge from years of experience that have them ready to make quick decisions when issues come up. So when should they reach out for help?
An important factor to understand is the difference between knowing how to purge a machine or resolve contamination issues, and knowing how to use a particular purge product. They are not the same, and unfortunately many have found this out after an appreciable amount of time has passed using a less effective solution. Here are some quick tips on helping you get the most from your purge supplier:
- Present as much data to your purge supplier as possible
- Purge suppliers often work very closely with production leaders to ensure that the purge solution is not only working efficiently but also to help ensure that the solution can be CLEARLY defined as a cost savings measure. The obvious reminder here, using a purge should net cost savings to the production, every single time. Defining the savings between a prior method and a prospective new method with a recommended purge product requires data and lots of it. What are the measurables that must be improved? Time and material quantities are a good start, but how does the production define the corresponding costs internally? In the end, purge solutions have been and always should be considered a cost savings project. What better way to plan and implement a cost savings initiative, if not to sit and look at actual and confirmed, you guessed it, “costs”? Make it clear what the goals and expectations are, and a purge supplier worth its weight will confirm the possibilities.
- Even if it’s possibly a purge issue, bring it up with your purge supplier
- As previously mentioned, production folks usually carry with them a few different areas of expertise, and many times they will first try to use their own knowledge and experience to solve an issue. Why ask for help or get others involved when you can do it yourself? A quick discussion can make a difference without stepping on any toes. Maybe the purge supplier has nothing to add or offer in certain cases, but now you know, and that confirmation is also useful knowledge. But what if the purge supplier suggests an approach that hadn’t been considered? Even if it doesn’t involve the use of purge? In the end, keeping the right experts at least in the loop can many times provide additional info and ideas, and that too is useful.
- The distinction between prior experience and unfamiliar products
- When faced with purge issues, it’s common for a production person to recall their first memories and experiences of a product, and quickly determine that “oh I’ve tried that before and it didn’t work”. Inversely, when recalling a positive experience they may incorrectly presume that the previous product from yesterday is the right product for today. Purge suppliers typically carry several different grades that can be applied under preventive or reactive purge strategies. It’s often forgotten that while an end user of a purge product may have had prior experience with a specific brand, they might forget that there can be a totally different solution from the same supplier ready and waiting for them. Please double-check with your purge supplier and avoid presumptions from prior experiences, good or bad.
Learn more about how to reduce production downtime and protect your profits with a purging compound.
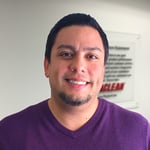
Celebrating his 24th year with Asaclean - Asahi Kasei Plastics North America, Lenny Gutierrez is a renowned purging expert who played a pivotal role in the company's expansion into Mexico in 2009. Currently, he excels as a Technical Sales Representative for Ohio, Illinois, and Missouri, combining his extensive industry knowledge with a strategic approach to drive sales and client relations. Lenny is also a prominent presenter at tradeshows and conferences, representing Asaclean with his expertise and professionalism.
Comments