Although your hold time is one of the most important stages of your cycle time, it is the one stage that often gets overlooked. Hold time comes during the second stage of a Decoupled-II process, which occurs after the first stage fills the cavity 95-98% full.
During the second stage, the hold pressure is used to completely fill the cavity and pack out any important complex detail or texture. The amount of hold pressure and hold time determine how much plastic is squeezed into the cavity and held until traditionally the gate freezes. This will determine the dimensions and weight of the part.
So how do we determine how much hold time is necessary? How do we know if we have excessive wasted time?
To do this you will have to perform a gate seal study.
You will need a running injection molding machine making good quality production parts. You will also need an accurate part scale in grams sensitive enough for two places behind the decimal point and your production parts.
How to Perform a Gate Seal Study:
Start out by setting your hold time to “zero” depending on how long your original hold time was. You may want to offset that reduction in cycle time by adding it onto your cooling time to keep a consistent cycle time and resin viscosity while performing this test.
With your hold time now at zero, you want to weigh your production part (fully trimmed, no gates, no runners).
Record that weight.
Increase your hold time by 0.5 seconds.
Wait one cycle then pull another part.
Record that weight.
Continue these steps increasing your hold time by 0.5 seconds and waiting a full cycle before pulling your next part.
Record the weight until your part weight stops increasing.
When your part weight stops increasing it means that the gate has finally sealed, and no more plastic can enter the cavity. This is officially your gate seal time.
Any less time means that the gate is not fully sealed which will allow for plastic discharge, variation and inconsistencies from shot to shot affecting weight and dimensions. Keep in mind, to molding variations like material, mold temperature, and plastic temperature, it is generally best to add an additional 0.5 sec’s to your hold time to guarantee gate seal. If you have not been adjusting your cooling time back along the way during this test, now is the time to put the cooling time set point back to the original setting.
Any additional hold time is wasted time draining the profits out of your production cycle. Performing a Gate Seal Study is a quick and effective way to determine the proper hold time which will help maximize your cycle efficiency.
Ready to reduce your production downtime to protect your profits? Learn more about how purging compounds and process efficiency work in tandem.
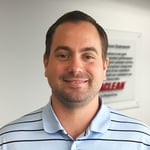
Hank Moeller is an Injection Molding and Purging Expert with over 20 years of experience in a processing environment.
Comments