If you run a molding or extrusion plant, your operations require a tremendous amount of energy. Throughout your manufacturing process, the resin works its way through your machine as it's melted and cooled.
- To transport it, vacuum pumps and air compressors are used to operate other equipment.
- To melt it, motors are used that turn the screws, and friction supported by some electrical resistances make the heat necessary to melt the pellet.
- Once the desired shape of the product has been achieved, it must be cooled to solidify it. This is one of the most important issues in plastics and ensures the reduction of cycles and therefore increases productivity. Chillers and other cooling equipment are used for this purpose.
Obviously, these all come with high-energy costs. With an uncertain economy, efficiency is more important than ever before. Here are some ways to make sure you're optimizing efficiency.
- In general, make sure your machine is in good working condition. If you've been cutting corners, it will cost you.
- Don't use a larger motor than is needed. Also, it might be more cost-effective to replace your motor than to repair an old one.
- Avoid leaks in your vacuum and compressed air systems.
- Regularly check to make sure you have clean filters.
- Similarly, check to make sure your chillers are the correct size and clean. If necessary, replace them with more efficient models.
After the above recommendations, you can also reduce the cost by keeping the power factor high with the use of capacitor banks.
Finally, the load factor must be monitored and maintained at high percentages. This can be achieved by phasing out machine start-ups. Asaclean can be used to seal barrels and molds so that the temperature increase is gradual. This will allow production to start up in a controlled manner, avoiding costly electricity demand peaks while meeting the plant's production requirements to the maximum.
We suggest starting first with the machines most needed for starting production, followed by machines that will start with low temperatures, and finally those that process high-temperature resins. This way, you will make the most of your time, electricity demand is gradual, you prevent the degradation of your resins, and above all, you make things easier and save money.
The same applies to companies with seasonality for whom it is advisable to work the first and third shifts, avoiding production during the hours when electrical rates are highest.
These actions will also have an impact on the planet by consuming energy efficiently.
Interested in starting your own preventative purge program? Request a free sample today and you'll be well on your way.
Learn more about how to reduce production downtime and protect your profits with a purging compound.
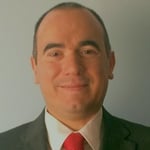
Hector Sanchez, the National Sales Manager at Asaclean - Asahi Kasei Plastics North America, leverages his extensive processing expertise to assist extruders and molders in achieving their operational goals. With a focus on reducing scrap and increasing profits, Hector's in-depth knowledge of Asaclean's Purging Compounds has made him a pivotal figure in the industry. Beyond his primary role, Hector is a dynamic speaker, regularly sharing his insights and strategies at webinars and tradeshows nationwide. His innovative approaches and dedication to customer success have established him as a valued leader and mentor in the plastic industry.
Comments