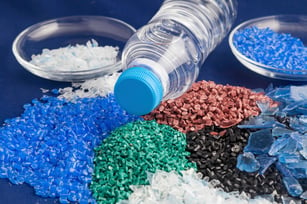
Your overall approach to purging impacts your ability to produce efficiently. For example, if you wait until you notice contamination in your finished product to clean your machines, the result is usually longer production runs and excessive machine downtime.
Preventive purging is a best practice for plastics processing companies working to reduce scrap rates. Additionally, taking a proactive approach improves operations and maximizes your bottom line.
Here are four preventive purging procedures to help you reduce scrap rates:
1. Use An Adequate Amount Of Purging Compound
Insufficient purging during downtime and changeovers is one of the most common causes of high scrap rates. When plastics processors don’t use enough purging compound, defect rates increase.
Some companies tell machine operators to use a specific amount of purging agent, encouraging a one-size-fits-all approach.
However, the required amount of purging compound for each changeover varies by situation. For example, the more time that has passed since a screw pull and manual cleaning, the more contamination you’ll see in your system.
Your supplier should train operators to purge until cleaning is complete, within a certain tolerance range, prior to contacting a supervisor. Placing a machine back into production after using a preset amount of purging compound is not advisable.
Overuse is also a potential issue here. You don’t want your operators using more purging compound than is necessary, because waste is the enemy of profitability. Overuse isn’t in anyone’s best interest.
2. Seal Your Machines During Shutdown
To prevent contamination, it’s important to seal your machine with a thermally stable purging compound during machine shutdowns and excessive downtime events such as PMs. Residual polymer degradation can delay machine startup and lead to excess material waste. Whether during a temporary or extended shutdown, sealing your machine is an essential step toward minimizing scrap rates.
3. Purge During Startups
At startup, extrude the sealing purge and follow up with one or two barrels of fresh purging compound before starting production. This aggressively removes contamination and carbon buildup that was pulled away from metal surfaces during sealing. Implementing this purge as part of your startup procedures helps reduce the time required to get up and running.
4. Purge Between Color And Material Changes
Whenever you change resins or materials, it’s critical that you purge your machines to remove previously run materials and protect against color contamination in your next batch. Although this is an additional step, the cost of including it in your purging procedures pales in comparison to the wasted materials caused by rejects.
Many plastics processing companies suffer from excessive material waste due to contamination during startup and changeovers. This is an unnecessary and avoidable cost. To avoid costly machine downtime and increased scrap rates, take a preventive approach to your purging procedures.
Learn more about how to reduce scrap rates in your injection molding machines.
Comments