To continue our conversation on how Injection Molders sell “Time,” we will transition from how blocking cavities will always increase your production lead time and decrease your profits to now focus mainly on the cycle time itself.
In my experience, cycle times are always being pushed to the limits. They get squeezed for every last tenth of a second you can get. However, if you are running a true Scientific Decoupled 2-3 molding process you know that it has been built from scratch for that machine, tool, and part design. All the parameters are finely tuned and interconnected to be able to run part-to-part consistently with tight tolerances. Therefore, making any parameter changes could be counteractive. If your process has not been built on such a detailed level here are some basic parameter changes to look at if you still need to squeeze another second or two from your cycle time.
If possible:
- Reduce your mold open position
- Increase, you Mold Open/Close speeds
- Reduce the amount of ejection strokes
- Increase your ejection forward/retract speeds
- Eject parts off on the fly
- Increase robot end of arm tool take out speeds
Now that some of the basics are out of the way here are two crucial key components of any cycle time: Hold Time and Cooling Time.
Let's first start with hold time. Theoretically, your hold time should not be any longer than the time it takes for your gate to seal. In order to determine this specific time, you will need to perform a Gate Seal Study. If you find that your hold time is drastically longer than your gate seal time, this could be wasted time that could be removed from you cycle time. You want to reduce that time to .5 seconds after the time it takes for gate to seal.
Second, let's look at cooling time. If you know your processing. You should know that the hold time is part of second stage cooling. Knowing this helps to understand and realize that your part only needs to be in the mold long enough for the part to cure and be structurally sound enough to be safely ejected from the tool. Any dimensional aspects of the part should have already been established with your pack/hold/cavity pressures then locked in with the gate seal. You can begin to reduce your cooling time in small increments until you find the line where the part starts having issues being ejected from the mold. Set your cooling time just about that line. This could be a place to further reduce cycle time only to be sure you are not affecting quality of the part.
Hopefully by taking a second look at some of your more basic post molding parameter set points you can find a little room for a quick pick up. Don’t forget to dig a little deeper and review your Hold Time and Cooling time to make sure they are set correctly for any additional one or two seconds of Cycle Time reduction while still producing good quality approved parts. Remember that any parameter changes always need to be documented and may need approval. Also, after making any parameter changes is always best practice to submit a part for full quality check.
Ready to reduce your production downtime to protect your profits? Learn more about how purging compounds and process efficiency work in tandem.
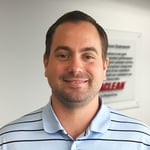
Hank Moeller is an Injection Molding and Purging Expert with over 20 years of experience in a processing environment.
Comments