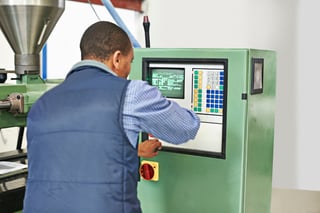
One of the most common defects in Injection Molding is the short shot. I remember many times that I was called to a machine to diagnose a short shot in the production run. At the time I worked in high cavitation thin-walled molding and short shots and flash were the 2 critical defects we had to really keep an eye out for in that production environment.
So what exactly are Short Shots?
Short shots or “shorts” are the incomplete filling of a mold cavity. Some shorts can be easily seen as a large part of the cavity missing and some are very small and hard to see with a visual inspection. Several factors can lead to short shots.
Many times shorts are related to a faulty process. Inadequate injection pressure or injection speeds can cause shorts. If the screw is bottoming out at the end of the cycle resulting in a zero cushion then the process can’t be relied upon as repeatable and many times this can generate shorts. If shorts are present in the production run the process should be checked as well as the resin being processed as a change in viscosity can throw off the process and cause defects in the production run.
The venting of the mold can also contribute to short shots. If the mold is not vented properly it is possible for the gas to not be able to escape the cavity in time for the molding cycle to complete. This can result in a short shot since the material can’t fill the void in the cavity because the gas hasn’t vented. The vents on the mold should be checked for blockages and repaired if needed.
Learn about the importance of implementing proper purging procedures by downloading this free industry guide.
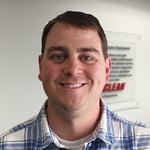
Jeremy Cooley is an Asaclean Technical Service Representative & Purging Expert living in South Carolina. He's worked in injection molding & purging for over 15 years, and frequently presents at national plastics trade shows and conferences.
Comments