Polymer Degradation is an injection molding defect that can be defined as change in the properties—tensile strength, color, shape, etc.—of a polymer or polymer-based product under the influence of one or more environmental factors such as heat, light or chemicals. Colors usually darken when degradation occurs and may range from yellow through orange to black, depending on the severity of the degradation. In this blog we will look at some causes of polymer degradation that arises from three factors – Machine, Mold, and Material.
1. Machine – The most common cause of material degradation is when the polymer in the barrel is overheated. This is the most basic cause for the defect and can be solved by reducing the melt temperature of the polymer. Temperature controllers can and will malfunction from time to time which can lead to a zone “running away” which simply means that the temperature is not being controlled correctly to the heater bands. Be sure that the correct type of thermocouple is being used for temperature control. Barrel residence time is extremely important in reducing the likelihood of polymer degradation. Obviously, the more time polymer spends in the barrel in residence the easier the polymer will degrade. Ideally you do not want your shot weight to be less than 25% of the shot capacity. Most processors shoot for 3-4 cycles for the polymer to go from feed throat to mold introduction.
2. Mold – If the shot weight of the mold is too small for the press that it is being ran in degradation can occur due to residence time in the barrel. If this is the case, the mold would need to be transferred to a machine with a smaller barrel capacity or volume.
3. Material – Polymer degradation can occur if the correct drying procedures for the specific polymer is not being followed. High moisture content of the plastic will cause the polymer to degrade faster than material that has been dried correctly. Also, if you are using regrind back into the system be sure that the quality of the regrind is sufficient for the process. Poor quality, contaminated, or multi generation regrind mixed with virgin material can promote degradation in the final melt.
Ready to reduce your production downtime to protect your profits? Learn more about how purging compounds and process efficiency work in tandem.
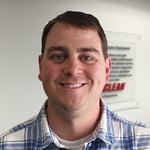
Jeremy Cooley is an Asaclean Technical Service Representative & Purging Expert living in South Carolina. He's worked in injection molding & purging for over 15 years, and frequently presents at national plastics trade shows and conferences.
Comments