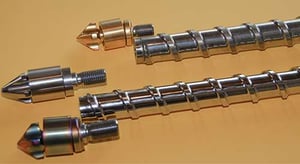
Most conventional thermoplastic molding machine injection units consist of a screw, non-return valve (NRV) and tip, housed within the barrel. The entire assembly reciprocates or is moving back and forth and is dual-functioning. Together, these components allow for plasticizing or building and then injecting the shot.
The NRV is a critical sub-assembly to this sequence of operation. The most common style is a check ring type. There are others available for specialized applications and materials which may be worth some further research. For this short blog we will focus on the most common.
When building a shot, as the screw rotates backwards, the check ring opens allowing for molten material to pass through flow channels and in front of the tip. Building up a pre-determined shot size within the barrel. When it comes time for injecting material, the entire assembly acts as a forward ram, simultaneously closing the check ring and flow channels, pushing forward the required material or shot. This occurs while also applying and maintaining plastic pressure within the mold.
The NRV and check rings (much like the screw and barrel components) are made from alloys or have surface coatings to reduce the effects of wear and extend the service life. However, after hours and weeks or years of run time, excessive wear (especially at the check ring) can become a point of concern. So, it is critical that this is considered and remains in the forefront of your machinery troubleshooting tool box.
One telltale sign you have a leaking or worn non-return valve is the machine losing its injection cushion and ability to apply plastic pressure. An improperly functioning NRV will have material slip past it and allows for the screw to encroach forward. This ends up limiting or making for poor control over consistent packing of the cavities. Creating difficulty in maintaining tolerances on the molded parts.
An early indicator of this processing issue is the presence of shot to shot variations. What may seem negligible at first, this will worsen over a relatively short time. At the next planned downtime opportunity it would be wise to disassemble and inspect NRV and components for wear, especially the check ring. Replace as necessary and you will return to making good quality parts, consistently.
The NRV area can also be a source for contamination. This is a notorious area for material to hang up or degrade. With a restricted flow through the valve openings, some shear action takes place here. This can be difficult to control or quantify (unlike a screw back pressure setting). Even a small amount of added shear heat can be the cause for localized degradation. It is also possible for color deposits from a previous run to remain hung up in this area. Both are an eventual cause for poor quality or rejected product.
One of the best ways to resolve this is by thoroughly cleaning the check ring between jobs or as needed. This can be accomplished by using some best practice purging methods and procedures. Include running short, high velocity shots with purging compound as you cycle the check ring multiple times. As a benefit, this will conserve the amount of purge being used while giving the best overall cleaning results.
If you would like additional information and some useful tips on maintaining machinery and best practice purging methods, please contact your Asaclean Technical Sales Representative.
Learn about the importance of implementing proper purging procedures by downloading this free industry guide.
Comments