If you are a packaging manufacturer processing PET, here’s a helpful tip to keep you rolling clean and clear while preventing teardowns.
I recently worked with a company experiencing severe contamination with heavy carbon showers during start and intermittently during production runs on a new sheet line they had just installed. During the trial run phase of this new product, the machine was constantly starting, stopping, or left sitting ideal under heat for long periods of time while waiting for the next shift or next small batch run. Also, this line was only running a few days out of the week in which case they would just run the machine empty and turn the heats off. Little did they know, they were their own worst enemy by causing all these contamination and carbon build-up problems themselves due to the lack of having a proper machine shut down procedure.
PET is a heat-sensitive resin and does not like to be held sitting ideal under processing heat for very long. You need to keep the material steadily moving through the system or it will begin to overheat, degrade, and break down eventually carbonizing over time creating the build-up and black spec carbon showers they were experiencing. Couple that, just running the system empty and simply flipping the heats off made things worse. It can take hours for large extruders to fully cool down.
Their current solution was to overhaul the system. Manually splitting the die and pulling the screw was taking them 2-days from disassembling to start-up. To make things worse, their poor procedures meant they'd spend time on reactive teardowns just to have the same issue come back weeks later. This is extremely labor-intensive and costly. Like an anchor to a hot air balloon, they simply could not get off the ground. It didn’t take long for them to reach out to us for help finding a solution.
We were happy to answer the call and recommended our NCR Grade to clean the entire system from the feed throat all the way out the die. Following our specific extrusion procedures and heating the system up to 550°F, we quickly began seeing all the carbon build up in the system they had caused come pouring out. We were breaking loose chunks of carbon so large they were getting stuck in the die lip gap which had to be increased. After running 150lbs of Asaclean NCR through a 4in. single screw extruder and 2hrs purging time, we were able to get a fully cleaned curtain of PET streaming out of the die. They had been down for days scratching their heads on how to prevent this from continuing to happen. We were able to save them from this vicious cycle that was draining them of much-needed production time and product delivery deadline promises.
Going forward, to prevent carbon build-up we recommended continuing using the Asaclean NCR-grade to purge clean, and stabilize the system during any long ideal periods but also as important to shut down and seal the machine with the NCR Grade during off-shifts, nights, and weekends when the machine is not scheduled to run. Our sealing procedures will stabilize and safeguard the machine when not in use to prevent the build-up from accruing. This allows this company to get back into production quickly and easily with confidence knowing their machine is clean and clear and they are properly maintaining the system.
Ready to reduce your production downtime to protect your profits? Learn more about how purging compounds and process efficiency work in tandem.
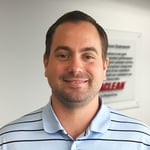
Hank Moeller is an Injection Molding and Purging Expert with over 20 years of experience in a processing environment.
Comments