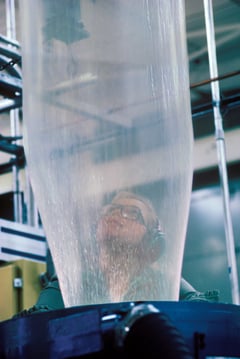
Purging compounds are essential for maintaining efficiency and minimizing downtime in thermoplastic processing. Are you using them to their full potential? This blog features a real-world injection molding case study, featuring practical insights and industry-specific tips to help processors optimize purging procedures and achieve cost-effective results.
The Importance of Documentation in Purging
To fully leverage the benefits of a purging compound, it's critical to document the following details:
- Grade Selection: Identify the purging compound that best meets the needs of your equipment and materials.
- Application: Specify when and where the purging compound should be used in your facility.
- Quantities and Methods: Record precise usage amounts and the recommended application techniques for consistent results.
Collaborating with your purging compound supplier can help you tailor a strategy that aligns with your production goals. Maintaining discipline in implementation—and being open to using multiple grades when necessary—can enhance efficiency. As processors know, "One tool can't solve every problem."
Case Study: Injection Molding with a Mechanical Purging Compound
Mechanical purging compounds were introduced in one facility to improve injection molding efficiency. Here's how the team optimized their use:
1. Selecting the Right Purging Compound:The team determined that a mechanical purging compound was ideal for their needs because:
- It offered a broad temperature range to handle various resins.
- It was compatible with hot runner systems.
- It could serve as a barrel seal during machine shutdowns.
2. Initial Implementation:
A small quantity of the compound was trialed. Early results showed significant reductions in downtime, but the team recognized opportunities to further improve consumption efficiency.
3. Identifying Key Adjustments:
During the training, adjustments to key machine parameters were identified:
-
- Lower RPMs: Reduced screw speed and backpressure minimized wear and material waste.
- Shot Size Optimization: Adjusting shot sizes from full-barrel to the minimum effective volume saved material without compromising cleaning performance.
Best Practices for Optimizing Purging Procedures
To maximize the compound's effectiveness, the facility conducted hands-on training for staff across several departments, including:
- Material Handling
- Process engineering
- Setup and maintenance
The training covered critical operational parameters such as RPMs, injection speed, backpressure, and shot size. Staff also received guidance on the recommended amount of purging compound for each machine size.
Standardizing the Process
The process engineer created a detailed purging procedure and tailored machine-specific guidelines. The documentation included:
- Recommended operating parameters for each machine.
- Maximum purging compound usage targets to prevent overconsumption.
Results: Increased Efficiency, Reduced Costs
By refining their approach, the facility achieved the same level of barrel cleanliness while reducing purging compound usage by nearly 50%, lowering material costs, and improving overall efficiency.
Take Your Purging Efficiency to the Next Level
Purging compounds play a critical role in reducing downtime, improving product quality, and maintaining consistent operations. If you'd like to explore how purging compounds can optimize your processes, we're here to help.
📧 Contact us to learn more about tailored solutions for your operation.
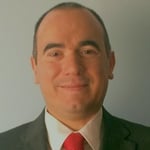
Hector Sanchez, the National Sales Manager at Asaclean - Asahi Kasei Plastics North America, leverages his extensive processing expertise to assist extruders and molders in achieving their operational goals. With a focus on reducing scrap and increasing profits, Hector's in-depth knowledge of Asaclean's Purging Compounds has made him a pivotal figure in the industry. Beyond his primary role, Hector is a dynamic speaker, regularly sharing his insights and strategies at webinars and tradeshows nationwide. His innovative approaches and dedication to customer success have established him as a valued leader and mentor in the plastic industry.
Comments