Hot runner manifolds are crucial in optimizing material utilization during injection molding. However, achieving their full potential requires more than just purging screws and barrels. This blog will explore effective methods to keep your hot runner system clean and ensure consistent quality.
The Challenge of Hot Runner Manifolds
Hot runner manifolds offer advantages like reduced material waste but can become a headache if not properly maintained. Recently, I collaborated with an automotive molder specializing in Nat. PP material using hot runner tools. Despite their diligent efforts to purge barrels and screws, they faced contamination issues and excessive scrap.
The Fear Factor: Purging Through Hot Runner Tools
The molder hesitated to purge through their hot runner tools due to concerns about sticking parts or damaging the steel. Unfortunately, this fear led to severe carbon buildup inside the manifolds. As a result, black specs appeared on the surface of their natural PP parts, causing high scrap rates.
The Missing Piece: Purging Through the Manifold
Purging screws and barrels is essential, but it’s only half the job. To maintain consistent quality, plastics must flow seamlessly through the manifold. Neglecting this crucial step can lead to costly consequences, as my client discovered when faced with gaylords full of scrap parts.
The Solution: PLUS Grade Concentrated Purging Compound
Our recent trials with the PLUS grade concentrated purging compound have yielded impressive results. This compound, mixed directly with your production material, offers several benefits:
- Effortless Moldability: Hot runner tools often allow easy molding with minimal processing parameter adjustments.
- Reduced Downtime: Automotive molders facing high production demands can’t afford extended machine downtime.
Trial Results: The Numbers Speak
We mixed the PLUS grade compound at 20% during the trial with their own Nat PP. The manifold temperatures were set at 450°F. When we started molding parts, they came out 90% filled, which was expected. This successful outcome demonstrates the effectiveness of the PLUS grade compound in maintaining optimal production quality.
The Soak Method: A Game-Changer
To tackle carbon buildup, we employed the soak method. After stopping the cycle, we let the purge sit and soak for three 5-minute periods, running 10 shots of parts between each soak. This allowed the PLUS grade compound to activate, loosen the carbon, and flush it out. The length of the soak period depends on the contamination level.
- First Soak: Carbon black specs poured out of the tool, confirming progress.
- Second Soak: Large chunks of carbon emerged, emphasizing the severity of the buildup.
- After just 10 shots, the system was completely flushed, and production resumed.
The Bigger Picture: Preventative Purging Programs
Automotive molders often focus on immediate demands, overlooking long-term tool maintenance. Properly maintaining the tool prevents future machine downtime and high scrap rates. Remember, hot runner manifolds are critical components—see the forest, not just the trees.
Conclusion
Maintaining hot runner manifolds is essential for maximizing efficiency and quality in plastic processing. By incorporating a comprehensive purging strategy, including the innovative use of PLUS grade concentrated purging compound and adopting preventative maintenance practices, manufacturers can significantly reduce waste and enhance productivity. Remember, effective maintenance is about seeing the forest for the trees—addressing not just the immediate but also the overarching needs of your production processes.
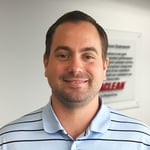
Hank Moeller is an Injection Molding and Purging Expert with over 20 years of experience in a processing environment.
Comments