Introduction
Screw pull, a mechanical cleaning method for injection molding machines, is often time-consuming and disruptive to production. This blog explores the hidden costs of screw pull and how a quality purging compound can significantly reduce the need for this process, saving manufacturers valuable time and money.
The High Cost of Screw Pull
While some companies lack the tools or personnel for screw pull, even those equipped face significant costs:
- Machine Downtime: Production halts while the machine is disassembled, cleaned, and reassembled.
- Labor Costs: Technician time dedicated to disassembly and cleaning.
- Equipment Risks: The potential for damage during disassembly and reassembly.
- Safety Risks: Potential for injuries during the maneuver.
Calculating the Impact
Consider the hidden costs of screw pull for your specific operation. How much production time is lost per screw pull? Factor in labor costs and the potential for downtime due to equipment damage.
Effective Purging as an Alternative
A high-quality purging compound, combined with a proper purging strategy, can effectively clean your machines, minimizing the need for screw pull. Asaclean offers a range of purging compounds designed to address specific needs, including those formulated to:
- Remove residual material: Ensure clean color and material changeovers.
- Improve machine efficiency: Reduce downtime and production delays.
Case Study: Reducing Downtime in Automotive Production
A client in Guanajuato, serving the automotive industry, faced mandatory annual screw pulls for wear monitoring on their 70 injection molding machines. The average cleaning process took 12 hours per machine, resulting in:
- Original Downtime: 70 machines * 12 hours/machine = 840 hours/year
The Asaclean Solution
Asaclean proposed a purging compound specifically designed to reduce cleaning time. Based on similar client experiences, this solution would significantly decrease cleaning time to 1 hour per machine, including disassembly and assembly.
- Reduced Downtime: 70 machines * 5 hours/machine = 350 hours/year
- Annual Savings: 840 hours - 350 hours = 490 hours
Calculate Your Savings
Imagine the increased production and profit potential with 490 additional hours of machine availability. Use this example to estimate the potential savings a quality purging compound can offer your operation.
Conclusion
By minimizing the need for screw pulls through a quality purging routine, Asaclean empowers plastic processors to achieve:
- Reduced Downtime: Free up valuable production hours and boost overall efficiency.
- Cost Savings: Eliminate the hidden costs associated with frequent screw pulls.
- Streamlined Operations: Simplify your maintenance procedures and keep your machines running smoothly.
Contact Asaclean today to discuss your specific purging needs and discover how we can help you unlock optimal production uptime.
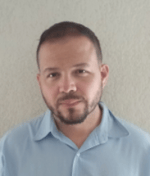
Mario De León brings unparalleled experience as a Technical Sales Representative for Mexico, with a career in the plastics processing industry spanning every key position, from materialist to injection molding management. With more than two decades of experience, Mario has mastered the art of team leadership by sharing the acquired knowledge with love and a desire for growth. Recognized for building lasting relationships in the industry, his dedication to improving clients' operations and driving success demonstrates his invaluable contribution to our team and the plastics industry.
Comments