The screw is one of the most vital components of an injection molding machine. For this blog we will consider a single screw general purpose variety since that is found in the majority of injection molding processes. It is the screw and the barrel that interact to convey, melt, and generate pressure within the plastic resin material. It is extremely important that this is done in a controlled way to produce the most consistent & uniformly plasticized material each and every time.
Assuming a general purpose screw; at the rear of the screw will be the drive shank to which the driving force is applied from the motor. Along the screw there are three sections; the feed section, the compression section, and the metering section. The feed section is located at the rear of the screw which is where the feed throat is located and where the resin will be introduced into the screw and barrel. The middle section of the screw is the compression section. The front of the screw is the Metering section. There are flights and channels along the length of the entire screw and the channel depth changes throughout the different sections of the screw.
The feed section starts at the rear and has a constant channel depth. The root diameter of the screw increases gradually from the end of the feed section to the start of the metering section where it becomes constant again (the larger the root diameter of the screw the less the channel depth will be).
The feed section is approximately 50% of the total length of the screw. The Compression section is about 30% of the length and the metering section is the remaining 20%.The flighted length of the screw is the overall length from the first flight in the feed section to the last flight at the tip of the screw. The flights are set at an angle to convey material forward and there will always be a leading edge of the flight and a trailing edge of the flight.
Sealing with Purge isn't the only way to reduce downtime. Learn more about how to reduce production downtime and protect your profits with a purging compound.
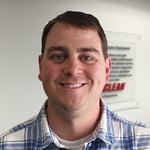
Jeremy Cooley is an Asaclean Technical Service Representative & Purging Expert living in South Carolina. He's worked in injection molding & purging for over 15 years, and frequently presents at national plastics trade shows and conferences.
Comments