Uninterrupted production is critical to maximizing efficiency in multifilament extrusion. However, clogged dies can disrupt your operation, leading to downtime and impacting your bottom line.
This blog post explores the causes of clogged dies in multifilament extrusion and offers strategies for keeping production lines running smoothly.
Understanding Clogged Dies in Multifilament Extrusion
Multifilament extrusion involves processing delicate filaments, often as thin as human hair. These filaments rely on clear and functional dies to maintain their integrity. Several factors can contribute to clogged dies:
- Contamination: Residual materials, degraded resins, or external contaminants can build up in the die, obstructing the flow of filaments.
- Temperature Fluctuations: Inconsistent temperatures can cause material breakdown or premature solidification within the die, leading to blockages.
- Worn Gear Pumps: Deteriorated gear pumps can struggle to maintain consistent pressure, leading to uneven flow and potential clogging.
The Impact of Clogged Dies
Clogged dies can significantly impact your operation:
- Production Delays: Blocked dies force production to halt for cleaning or maintenance, impacting your output and delivery schedules.
- Machine Downtime: Clearing clogged dies requires disassembling the extrusion line, costing valuable production time.
- Wasted Resources: Scrapped filaments and purging attempts can lead to wasted materials, increasing operating costs.
Strategies to Prevent Clogged Dies
- Consistent Monitoring: Regularly monitor pressure gauges and temperature controls to identify potential issues before they lead to blockages.
- Preventative Maintenance: Implement a regular maintenance schedule to clean dies and replace worn components like gear pumps.
- Filtration Systems: Utilize filtration systems upstream of the die to remove contaminants from the resin before it reaches the delicate filaments.
Optimizing Your Process with Purging
While preventative measures are crucial, a purging program can offer additional benefits:
- Enhanced Flow: Periodic purging helps remove residual materials that might accumulate and impede filament flow.
- Efficient Changeovers: Purging facilitates smoother transitions between colors or resin types, minimizing waste and production delays.
Choosing the Right Purge
Selecting the most effective purging solution requires considering factors like compatibility with your equipment and materials. Our customer uses concentrate purge grades, Asaclean PLUS, which can be mixed directly with your production resin. These concentrate grades provide several advantages:
- Efficient Cleaning: They effectively clean your machine without causing blockages themselves.
- Reduced Waste: They can help streamline your process and reduce waste by minimizing the need for separate purging runs.
Consulting with a qualified purging expert can help you explore the different options available and identify the most suitable solution for your specific needs. This ensures you find a purge that effectively cleans your equipment while aligning with your existing processes.
Conclusion
Understanding the causes of clogged dies and implementing preventative strategies can significantly reduce the risk of disruptions in your multifilament extrusion process. Regular monitoring, proper maintenance, and a well-designed purging program can all contribute to keeping your production lines running smoothly and efficiently.
Consult us today for further information on purging solutions and how they can benefit your multifilament extrusion operation.
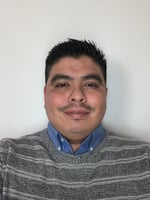
Lazaro Estrada, a skilled Technical Sales Representative for Mexico at Asahi Kasei, has a distinguished engineering and process optimization background. Before joining Asahi Kasei, he was instrumental in developing projects with clients for the selection and implementation of injection and die-casting machinery, including overseeing their installation and startup of new processes. Holding a professional degree in Electronics with a specialization in automation, Lazaro's career has been defined by his leadership in project development, ranging from chemical industry reactors and synthesis to machinery and continuous improvement in the plastic industry. His expertise and forward-thinking approach make him a key resource for clients aiming to advance their operational capabilities.
Comments