A Virginia-based manufacturer specializing in lightweight roofing sheets and panels faced ongoing contamination issues while extruding rigid PVC and Polycarbonate (PC). Contamination compromises product quality and escalates maintenance costs and downtime, impacting overall production efficiency. This blog post explores their journey towards enhancing production efficiency, highlighting effective strategies, and sharing quantifiable outcomes.
Understanding Contamination in Sheet Extrusion and PVC Processing
Contamination is a significant hurdle in sheet extrusion and PVC processing, particularly with rigid PVC and polycarbonate materials. These materials are prone to build-up on screws, barrels, and dies/tooling, which can lead to carbon contamination. This results in diminished product quality, increased downtime, material waste, and escalating maintenance costs.
Strategies for Tackling Contamination
The manufacturer explored several strategies to address these challenges, including trialing different purging compounds. Asaclean C Grade was included in these trials and was found to be particularly effective, tailored to their specific material needs.
Collaborative Approach to Problem Solving
At Asaclean, we emphasize a partnership approach. We conducted an on-site assessment with the manufacturer and worked closely with their team to customize a purging program. This collaboration ensured that the solution was effectively integrated into their existing processes.
Quantifiable Improvements in Production
After implementing Asaclean C Grade, the manufacturer experienced significant improvements:
- Material Usage: The average usage of in-house purge material decreased from 80 lbs to only 20-25 lbs.
- Reduced Downtime: Downtime associated with purging was cut from 2 hours to approximately 1 hour.
- Decrease in Waste: The number of scrapped panels was reduced from 80 to just 12-15 per batch, enhancing cost efficiency and reducing waste.
Tips for Manufacturers
For manufacturers facing similar issues, consider the following tips:
- Regular Maintenance: Maintain equipment regularly to prevent contaminant build-up.
- Trial and Evaluate: Experiment with different purging compounds to find what best suits your needs.
- Seek Expert Advice: Utilize consultations from experts who can offer tailored solutions and hands-on trials to optimize your processes.
Conclusion
Effectively managing contamination in sheet extrusion and PVC processing is pivotal for enhancing production efficiency and maintaining high product quality. By understanding your challenges and exploring various solutions, you can make informed decisions that significantly impact your bottom line. At Asaclean, we are dedicated to supporting your endeavors with our expertise and a commitment to achieving the best outcomes.
Consult us today for further information on purging solutions and how they can benefit your multifilament extrusion operation.
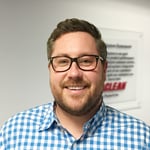
Ben Moore brings over 20 years of experience as a Purging Expert at Asaclean Purging Compounds, a leading manufacturer and distributor of purging compounds. As part of Asahi Kasei Plastics North America, Inc. (APNA), Ben has personally assisted hundreds of customers, helping them achieve significant cost savings. Based in Parsippany, NJ, Ben specializes in optimizing operations for thermoplastic injection molding, extrusion, compounding, and blow molding processes. His expertise lies in maximizing production efficiency by minimizing downtime and reducing scrap. For those interested in trying Asaclean products or seeking expert guidance, feel free to contact Ben directly. You can contact him at 800-787-4348, extension 227, or via email at bmoore@asaclean.com.
Comments