Contrary to popular belief, you should never perform shots at 100% when purging an injection molding machine.
The notion that the larger the shot, the more cleaning power you have, is outdated. Additionally, it leads to much higher purge consumption. Many processors also think that using a larger amount of purge will achieve greater cleaning. This could not be further from the truth. This may be surprising coming from someone who sells purge, but we want you to have the best performance using the least amount of purging compound necessary to achieve that performance. Purge is meant to dramatically improve efficiency. Using your purge inefficiently defeats the purpose.
Efficient purging requires discipline and adherence to official instructions, rather than following purging traditions that possibly were learned with different products many, many years ago. One of these traditions is to purge with 100% shot size or using the auto purge function, often without ensuring that you have adapted the function to the procedure for your purge compound.
In most molding machines, the auto purge function charges full shots performed at slower speeds. When using mechanical purging compounds, it is important to verify that the auto purge function perform the correct process, as is the case with Asaclean’s short-shot recommendation (which is only one part of the official procedure): perform short, repeated shots with high injection speed. Take into account that the auto purge function usually does not allow for maximum back pressure and thus even if adapted to perform short shots, this would not cover the entire procedure that contributes to cleaning performance. Always refer to your purge product’s official instructions. To be clear, in most situations, auto purge functions won't get the most out of your purging compounds. Do not assume that your program will match the purge instructions.
I am all for being resourceful and for trying to fix things. But in this one area, a high-quality purging compound like Asaclean makes your life much easier without headaches or ongoing trial-and-error. After I visited this customer's plant and built them a purge program, they started having painless start-ups without scrap or downtime.
Now, let’s try to imagine what happens inside the barrel to help make a better decision of which method to use. When charging a full shot, imagine a cylinder-shaped quantity of purge created in front of the screw, and when the shot is injected the center of this cylinder is pushed right out of the machine in one fell swoop. All of that purge quantity exits the machine with just one movement of the check ring without giving the purge the best opportunity to scrub and clean. On the other hand, performing short shots allows the purge to move the valve many more times (using the same amount of purge created with one full shot) and helps generate pressure changes in the nozzle area using more efficiently the amount of purge fed, and thus drastically reducing the purge quantity required.
This recent example during a change from ASA resin to polypropylene demonstrated the same usage reduction benefit. Purging a 350 ton machine, four kilograms of purge was used and rejects with ASA resin contamination continued in the next polypropylene run. The lack of cleaning allowed for ASA resin to stay lodged in the machine, and showed up in the following pp parts causing breakage. After receiving the client's report and a quick review of the procedure, the above-mentioned corrections to the procedure were applied. The result? They only required a kilogram and a half of purge, a mere 38% of what was consumed before, and even better, the rejects due to breakage were eliminated.
Ready to reduce your production downtime to protect your profits? Learn more about how purging compounds and process efficiency work in tandem.
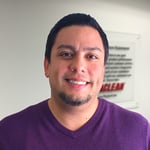
Celebrating his 24th year with Asaclean - Asahi Kasei Plastics North America, Lenny Gutierrez is a renowned purging expert who played a pivotal role in the company's expansion into Mexico in 2009. Currently, he excels as a Technical Sales Representative for Ohio, Illinois, and Missouri, combining his extensive industry knowledge with a strategic approach to drive sales and client relations. Lenny is also a prominent presenter at tradeshows and conferences, representing Asaclean with his expertise and professionalism.
Comments