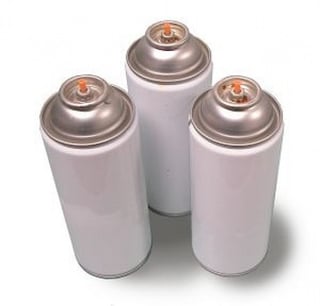
Many years ago, I performed a trial at a Midwest Injection Molding company.
They asked me to troubleshoot a knit line problem with a part that was being produced from Vectra A-130 (LCP) resin. For those not familiar, Vectra inherently has poor knit line strength. The part was a 10” long probe, approximately 3” in diameter with a thick wall thickness of about 0.100”. It was gated in such a way that it caused a knit line on the opposite side of the gate.
First off, I discovered that the old Cincinnati Milacron machine I was working had a leaky check ring and I could not pack the part out properly. This caused a poor weld/knit line to form. Once the machine was fixed and the tech was producing parts, I noticed him spraying mold release on the core for the part to release.
This was where the mold release became detrimental to the process. They used so much mold release that the Vectra flow front was pushing the release along the core and trapping it in the weld/knit line, thus producing rejected parts.
The solution was easy. With a new check ring in the machine, we stopped using mold release and we made some simple adjustments to the tool to help it release. Once these two steps were taken, we were producing great parts with strong weld lines and no rejects.
Learn about the importance of implementing proper purging procedures by downloading this free industry guide.
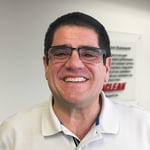
Eric Despotovich, an esteemed Asaclean Purging Expert and Technical Sales Representative, brings over 40 years of processing experience to his role. With over 18 years of dedication to our company, Eric has become a cornerstone of our sales team, renowned for his commitment to client success. His extensive industry knowledge and genuine passion for helping clients make him a trusted advisor in optimizing their operations. Eric's approach is characterized by deeply understanding each client's unique challenges, ensuring tailored solutions that drive efficiency and profitability.
Comments