“How often should we purge,” “How much quantity of purging compound should we use,” and “How should the purge compound be used” are a few oft-asked questions we field from the end users of our injection molding and extrusion customers. They are great questions and should be asked of the supplier. Odds are likely that you might know what I am talking about and have been asked these before.
So, the questions above are answered by training with some regularity. Train, train, train…then train some more.
These are my top reasons why routine purge training on production floors is necessary and should be obligatory. Let me tell you why:
- It provides principle and purpose to the end users and helps them better understand why they are using a compound and how it benefits them.
- It better educates and arms the end user with the right knowledge on proper usage, purge quantity used, and realistic frequencies. This put them on a constructive path that achieves the best possible results using the least amount of purging compound. As an added benefit, when the end users are trained on correct usage, they also learn how it should not be used.
- It naturally helps your plastic company with best practices, continuous improvements, and sustainability. It helps develop and form more confidence in themselves and the purging product itself. Furthermore, it gives them deeper involvement in their organization while helping them to realize how they can be a part of their company’s prosperous future growth.
Purge compound training is good, all-around, for all. It is good for everyone, from seasoned veterans to brand-new hires and everyone in between. You know the saying, “Practice Makes Perfect”? Well, I would like to take that one step further with “Purging Practice Makes Perfect.”
Ready to get your production team well-trained and implement a comprehensive purge training program?
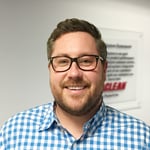
Ben Moore brings over 20 years of experience as a Purging Expert at Asaclean Purging Compounds, a leading manufacturer and distributor of purging compounds. As part of Asahi Kasei Plastics North America, Inc. (APNA), Ben has personally assisted hundreds of customers, helping them achieve significant cost savings. Based in Parsippany, NJ, Ben specializes in optimizing operations for thermoplastic injection molding, extrusion, compounding, and blow molding processes. His expertise lies in maximizing production efficiency by minimizing downtime and reducing scrap. For those interested in trying Asaclean products or seeking expert guidance, feel free to contact Ben directly. You can contact him at 800-787-4348, extension 227, or via email at bmoore@asaclean.com.
Comments