Before the rise of commercial purge compounds, many production floors relied on using the same resin for purging machines or manually pulling the screw before each critical production run. While purge compounds are designed to clean thermoplastic process machinery more efficiently, some straightforward purge needs can be addressed with resin alone. However, this option comes with certain limitations and risks.
Understanding Resin Purging
For low-difficulty purging applications, production often chooses a resin with equal or higher viscosity. This choice leverages the "viscosity push" provided by the resin. However, relying solely on resin for purging presents several challenges:
-
Layering and Carbonization: A common issue with resin purging is layering, which can leave resin in the machine and hide polymer deposits. Over time, this can lead to carbonization, causing carbon specks and contamination.
-
Limited Reach: In low-flow and low-pressure areas on the screw and tooling, resin lacks the expanding properties of some commercial purge options. This limits its ability to reach and clean hang-up spots, often requiring a larger quantity of resin without fully addressing the root problem.
-
Cost Implications: The cost of using resin for purging can be significant. Many overlook the total cost by focusing only on the price per pound and not the total pounds used. This raises the question of whether using a purpose-designed purge compound might result in substantial savings.
Advantages of Using Purge Compounds
Commercial purge compounds offer several benefits over resin purging:
- Increased Production Time: Purge compounds can quickly clean machines, increasing available machine and production time.
- Efficient Cleaning: They require less material for effective cleaning, reducing waste.
- Higher Resin Yield: Using purge compounds can lead to higher yields of saleable products.
For those focused on producing quality parts from the start, maintaining a clean machine is crucial, and using a purge compound is often the optimal solution.
When to Use Resin or Purge Compounds
The type of job will determine how critical it is for a machine to be thoroughly clean. Some customers even require a screw pull to verify a contamination-free process. A purge supplier offering a range of options—from resin to high-powered purge grades—can be invaluable when reviewing a purge program.
Purge “resin” is also available from our product line for circumstances where purging with resin only is adequate. Please reach out to us for purge compound recommendations and to inquire about resins to be used as purge. We can review and confirm the best options for your needs.
Learn More
Discover how to reduce production downtime and protect your profits with a purging compound. Contact us for expert advice and tailored solutions.
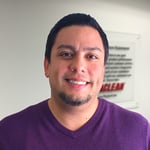
Celebrating his 24th year with Asaclean - Asahi Kasei Plastics North America, Lenny Gutierrez is a renowned purging expert who played a pivotal role in the company's expansion into Mexico in 2009. Currently, he excels as a Technical Sales Representative for Ohio, Illinois, and Missouri, combining his extensive industry knowledge with a strategic approach to drive sales and client relations. Lenny is also a prominent presenter at tradeshows and conferences, representing Asaclean with his expertise and professionalism.
Comments