Energy costs are one of the most significant expenses in plastic manufacturing. Plastic processors rely on energy-intensive equipment, from transporting materials to melting and cooling processes, to maintain production efficiency. Understanding how to optimize energy usage can lead to significant cost savings and improved sustainability.
Why Energy Consumption is High in Plastic Processing
Plastic processing requires large amounts of electricity due to several key operations:
- Material Transport: Vacuum pumps and air compressors are essential for moving materials and operating auxiliary equipment.
- Melting Process: Motors drive screws to generate frictional heat, which, combined with electric heaters, melts plastic pellets.
- Cooling Process: Once a product is shaped, it must be cooled quickly to solidify. Chillers and cooling systems are crucial in reducing cycle times and improving productivity.
Each process contributes to high energy consumption, but plastic processors can improve efficiency and lower costs with the right strategies.
Practical Ways to Reduce Energy Costs
To minimize electricity usage, manufacturers should focus on efficiency improvements in equipment and processes.
- Maintain equipment Regularly: Ensure all machinery is in optimal working condition to prevent energy waste.
- Use Properly Sized Motors: Oversized motors consume more electricity than necessary. If a motor is outdated, replacing it with a more efficient model may be more cost-effective than repairing it.
- Prevent Air and Vacuum Leaks: Leaks in compressed air and vacuum systems lead to wasted energy. Regular inspections should be conducted to detect and fix leaks.
- Keep Filters Clean: Clogged filters in pumps and air systems reduce efficiency and increase energy demand.
- Optimize Cooling Systems: Chillers should be appropriately sized for your operation. Consider upgrading to energy-efficient cooling equipment.
Managing Power Demand to Cut Costs
Beyond improving efficiency, the power demand should be strategically managed to avoid unnecessary peak charges.
- Maintain a high power factor by using capacitor banks to reduce energy waste.
- Monitor and optimize load distribution by staggering machine startups.
How Purging Compounds Help Reduce Energy Costs
One often-overlooked way to lower energy consumption is through purging compounds like ASACLEAN®. By purging compounds to seal barrels and molds during startups, processors can gradually increase machine temperatures, preventing sudden energy spikes that drive up electricity costs.
Recommended Machine Startup Strategy
To optimize energy use, stagger machine startups in this order:
- Start machines needed for urgent production first.
- Bring lower-temperature processing machines online next.
- Finally, start machines that process high-temperature resins.
This approach reduces sudden demand surges, prevents resin degradation, and enhances overall operational efficiency—leading to lower electricity costs.
Avoiding Peak Electricity Rates
For companies with seasonal production variations, energy savings can be maximized by scheduling production during lower-cost electricity hours. Operating primarily during the first and third shifts can help avoid peak-time electricity charges, reducing costs.
Conclusion: Energy Efficiency Benefits Your Bottom Line
Plastic manufacturers can reduce operational costs, improve productivity, and contribute to sustainability by implementing these energy-saving best practices. Purging compounds like ASACLEAN® play a key role in managing energy usage efficiently, helping processors maintain stable operations while lowering electricity expenses.
Want to learn more about how ASACLEAN® can optimize your production? Contact us today!
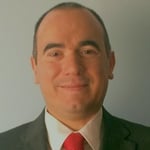
Hector Sanchez, the National Sales Manager at Asaclean - Asahi Kasei Plastics North America, leverages his extensive processing expertise to assist extruders and molders in achieving their operational goals. With a focus on reducing scrap and increasing profits, Hector's in-depth knowledge of Asaclean's Purging Compounds has made him a pivotal figure in the industry. Beyond his primary role, Hector is a dynamic speaker, regularly sharing his insights and strategies at webinars and tradeshows nationwide. His innovative approaches and dedication to customer success have established him as a valued leader and mentor in the plastic industry.
Comments