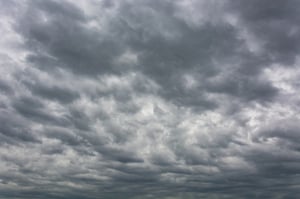
Haziness or cloudiness in molded parts is one of the most common injection molding defects. When beginning Purge Programs with customers, I'm often asked how they can eliminate the presence of cloudiness or haze in molded parts. Most often this problem occurs when parts are being made with colored, semi-transparent resins, or have optically clear requirements. When this defect is present, it can be a stubborn one to fully resolve. Unfortunately, this means a pile of scrap, poor quality rejected parts, and lost machine time.
A primary cause and one of the first things to look for the presence of contamination. Always check the hopper and material feed areas to make sure they are clean. Within the molding machine, the causes can be a buildup of color or carbon deposits. Contamination is likely to come from material still being present in the machine or hopper from the previous run.
This is especially true when going from olefins (such as polypropylene or polyethylene) into a styrene, polycarbonate or other translucent or transparent type resins. The residue left behind will almost always appear as milky streaks but can also show up as cloudiness or haze. If this is found to be the cause or is at least suspect, it will save time and money in the long run to fully complete an effective purge by following an established purging procedure between the material change. Consult with your purging compound supplier for the optimum grade needed in this scenario.
While investigating the hopper and feed areas, be sure to check that the dryer is on and functioning correctly. Make sure that there is proper air flow. A quick way to check is the inlet and outlet hoses by hand. This will give you an idea of if the dryer is working properly. Note the temperature feel. Consult your production material suppliers molding guide. Then look over the dryer set points. You may find that there’s a need to increase the drying time and or the temperature for the type of material being run.
If after completing the above the defect is still persistent, look at the barrel temperature profile. Increase the melt temperature staying within the manufacturers recommended range. This can be done by increasing the barrel zone set points. Alternatively melt temperature can be increased by raising the machines back pressure setting. Somewhat related, using increased injection pressure is another option that can similarly help to resolve the defect.
Mold temperature can also be a factor. If set too low, it can cause this defect. Raise the temperature, incrementally. Once at desired temperature check to see that the defect has went away. As with raising the back pressure, when raising mold temperature, it is important to consider staying within the overall quoted cycle time for the part being run.
If you would like more information on implementing an effective purge program and resolving this or any other processing related defects, Asaclean Technical Sales Representatives are highly experienced and available to assist you. As always, our objective is to support your objectives, for maximizing production efficiency, by reducing or eliminating machine down time and scrap!
Learn about the importance of implementing proper purging procedures by downloading this free industry guide.
Comments