Throughout my years of visiting various plastic processing plants, I've noticed a common thread among them, regardless of the type of process or industry they belong to. These facilities share objectives such as continuous improvement, greater profitability, customer satisfaction, a safe working environment, and regulatory compliance. However, when asked what resource, tool, technique, or equipment would make the most significant difference in their operations, the overwhelming response is consistently "Trained Personnel." In this blog, we'll explore why a skilled workforce is the #1 factor in achieving efficiency and success in plastic processing and how you can maintain it, even in challenging circumstances.
- Invest in Hands-On Training:
Hands-on training is one of the most effective ways to develop a skilled workforce. Learning from experienced individuals within the industry can provide invaluable insights and practical knowledge. Encourage your team to actively participate in training sessions and workshops to improve their skills. - Leverage Supplier and Customer Expertise:
Pay attention to the wealth of knowledge your suppliers and customers can offer. Collaborate with your suppliers to arrange training visits, allowing your team to learn about new materials, techniques, and equipment. Additionally, if the opportunity arises, let your customers teach you how to enhance your product or service. Their insights can be a game-changer. - Document Best Practices:
In today's digital age, capturing and sharing best practices is easier than ever. Consider recording video tutorials of your most experienced employees showcasing their skills. These videos can serve as valuable training resources for new hires and as a reference for existing staff. - Establish Partnerships with Schools:
To address workforce challenges, consider establishing partnerships with local educational institutions. Offer access to internships and, in return, request continuing education programs for your employees. This symbiotic relationship can help you secure a pipeline of skilled workers for the future. - Streamline Training Processes:
Keep your training process simple and effective by following these steps:
a. Identify processes and the required "know-how" for each.
b. Recognize skill deficiencies among your team.
c. Develop a cyclical training plan to reinforce knowledge and best practices.
d. Execute the training plan consistently.
e. Evaluate your staff's performance in real work situations, providing valuable feedback to employees and the training system.
In Conclusion:
A capable and skilled workforce is the #1 factor in achieving success in plastic processing. Investing in employee training and development is essential for driving efficiency, consistency, and long-term success in your operations.
At Asaclean, our training programs are designed to elevate your staff's expertise in purging procedures to new heights. Contact us today to discover how our training can benefit your organization.
By prioritizing the development of your personnel, you'll be better equipped to meet your objectives, improve profitability, enhance customer satisfaction, maintain a safe working environment, and ensure regulatory compliance in the competitive world of plastic processing.
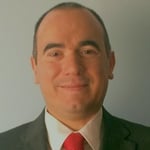
Hector Sanchez, the National Sales Manager at Asaclean - Asahi Kasei Plastics North America, leverages his extensive processing expertise to assist extruders and molders in achieving their operational goals. With a focus on reducing scrap and increasing profits, Hector's in-depth knowledge of Asaclean's Purging Compounds has made him a pivotal figure in the industry. Beyond his primary role, Hector is a dynamic speaker, regularly sharing his insights and strategies at webinars and tradeshows nationwide. His innovative approaches and dedication to customer success have established him as a valued leader and mentor in the plastic industry.
Comments